Central Mount |
Holds the blades securely, ensuring stability during operation. |
Maintenance Guide for Optimal Performance
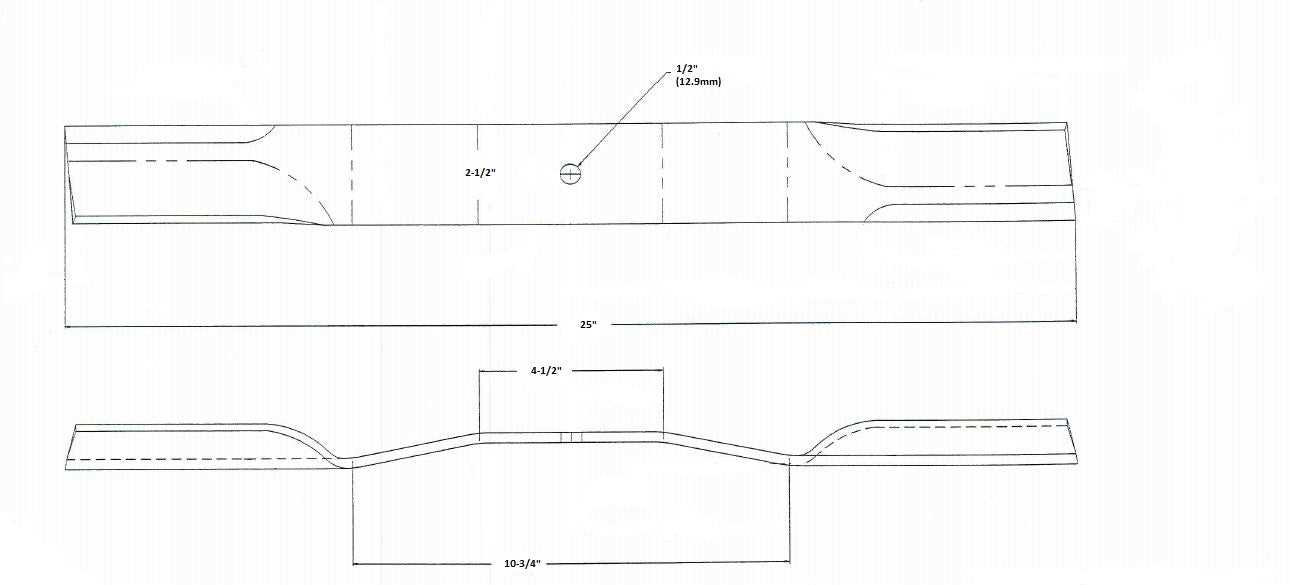
Regular upkeep is essential to ensure the machinery functions efficiently over time. Proper attention to detail during inspections and servicing can prevent wear and tear, extend the lifespan, and guarantee smooth operation. Following a structured approach to maintenance will help avoid unexpected breakdowns and ensure that the equipment remains reliable.
Routine Inspection
It’s critical to perform routine checks on all mechanical components to detect any early signs of damage. Focus on the areas most prone to friction or pressure, as these parts often require additional care. Tightening loose fittings, lubricating moving components, and replacing any worn-out pieces will keep the system running smoothly.
Cleaning and Lubrication
Accumulated debris can hinder performance, making regular cleaning a priority. Removing dirt and build-up from key mechanisms will ensure that the machinery operates without obstruction. Additionally, applying the proper lubricants to moving parts will reduce friction, minimize wear, and maintain efficiency.
Preventative maintenance is the key to avoiding costly repairs and ensuring longevity. By following a consistent schedule of cleaning, lubrication, and inspection, you can ensure optimal performance and prevent unnecessary downtime.
Common Replacement Parts for Long-Term Use
Over time, frequent usage and exposure to varying environmental conditions can lead to wear on essential components. To ensure continued efficiency and prevent unexpected breakdowns, it is vital to identify and replace certain elements that experience the most stress and wear. These components are designed to endure demanding conditions, but regular maintenance and timely substitution can significantly prolong the operational life of the machine.
Blades and Cutting Edges
The cutting system is often the first to show signs of deterioration. Regular inspection and sharpening can extend its usability, but eventual replacement is inevitable to maintain optimal cutting performance. Ensuring that sharp edges are intact will also reduce strain on the equipment, improving overall efficiency.
Bearings and Gear Assemblies
Another critical area for long-term upkeep is the system of bearings and gears. These components are responsible for smooth motion and power transfer. Over time, the constant rotation and mechanical pressure can cause them to lose efficiency. Replacing worn or damaged parts will help maintain seamless operation and prevent costly repairs in the future.
Troubleshooting Issues with the ATH 720
When operating heavy machinery, encountering problems is not uncommon. Identifying and resolving these issues promptly can ensure optimal performance and longevity of the equipment. This section aims to guide users through common challenges, providing insights on how to effectively troubleshoot and maintain their machinery.
Identifying Common Problems
Users may face a variety of issues, from unusual noises to decreased efficiency. The first step is to conduct a thorough examination of the equipment. Pay close attention to any signs of wear or malfunction, such as:
- Inconsistent operation
- Overheating components
- Leaking fluids
Documenting these observations will help in diagnosing the root cause of the problem.
Steps for Effective Resolution
Once potential issues are identified, follow these steps to address them:
- Consult the Manual: Refer to the operational guide for troubleshooting tips specific to your model.
- Perform Regular Maintenance: Regular checks can prevent small issues from escalating into major problems. Keep all moving parts lubricated and clean.
- Seek Professional Help: If the issue persists after your troubleshooting efforts, consider contacting a qualified technician for assistance.
By being proactive and attentive to your machinery’s needs, you can minimize downtime and enhance its performance.
Buying Genuine Components for Repairs
When it comes to maintaining machinery, sourcing authentic elements is crucial for ensuring optimal performance and longevity. Utilizing original equipment can prevent potential issues that may arise from inferior substitutes. This section explores the importance of selecting genuine items when making repairs.
Benefits of Genuine Items
- Quality Assurance: Authentic components are designed to meet the exact specifications of the original equipment, ensuring compatibility and reliability.
- Longevity: Investing in genuine items often results in extended lifespan and durability, minimizing the need for frequent replacements.
- Warranty Coverage: Using original components typically preserves the warranty of your machinery, safeguarding your investment.
Where to Find Authentic Components
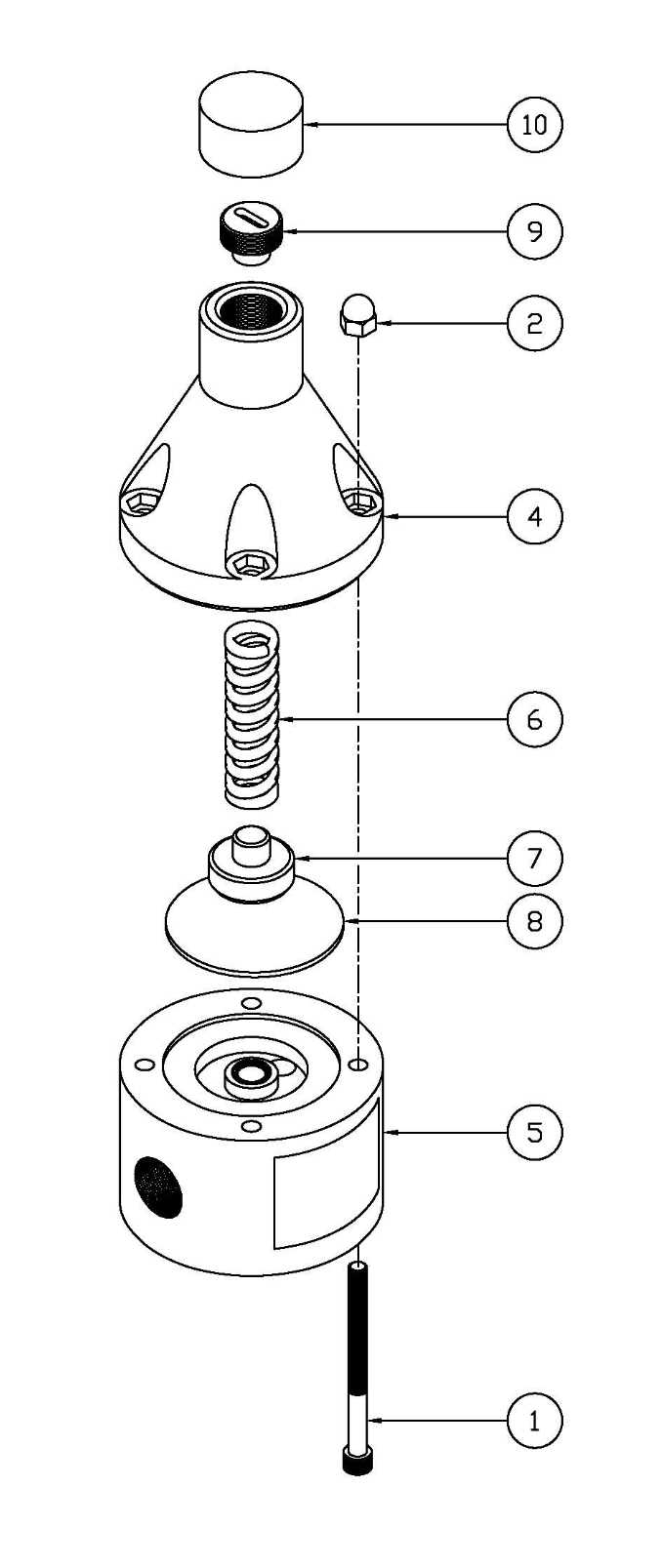
- Authorized Dealers: Purchase from certified vendors to guarantee authenticity and quality.
- Manufacturer Websites: Check the official website of the equipment manufacturer for direct sales or recommended suppliers.
- Reputable Online Retailers: Look for well-known online platforms that specialize in genuine replacement items.
How to Identify Worn-Out Parts
Recognizing the signs of deterioration in equipment components is crucial for maintaining optimal performance. Various indicators can help you determine whether a component has reached the end of its useful life. Understanding these signs allows for timely replacements, preventing further damage and ensuring efficiency.
Visual Inspection
Start with a thorough visual examination of the equipment. Look for the following:
- Cracks and Fractures: Check for any visible cracks that may compromise integrity.
- Corrosion: Look for rust or signs of oxidation, which can weaken metal components.
- Wear Patterns: Identify uneven wear, which can indicate misalignment or other issues.
Performance Assessment
Monitoring the functionality of equipment is equally important. Consider the following aspects:
- Unusual Noises: Listen for strange sounds that may indicate mechanical issues.
- Decreased Efficiency: Note any decline in performance, such as slower operation or reduced power.
- Frequent Breakdowns: Pay attention to recurring failures that could signify underlying problems.
By combining visual assessments with performance observations, you can effectively identify components that require attention, ensuring your equipment remains in top condition.