Check oil level |
Identifying Wear and Tear in Parts
Understanding the signs of deterioration in components is essential for maintaining equipment efficiency and safety. Regularly inspecting for damage or excessive wear can help ensure that machinery operates optimally and can prolong its lifespan. Recognizing these indicators allows users to take timely action, preventing further issues that may arise from neglected maintenance.
Common signs of deterioration include:
- Cracks or Fractures: Look for visible cracks on surfaces, which may indicate weakness or structural failure.
- Worn Edges: Check edges for rounding or excessive wear, affecting cutting performance and precision.
- Loose Connections: Inspect joints and fittings for looseness, which can lead to inefficient operation or even accidents.
- Discoloration: Notice any unusual color changes, which may suggest overheating or material degradation.
- Rust or Corrosion: Identify any signs of rust, especially on metal components, indicating potential failure points.
Regular maintenance checks should include examining each part for these signs. Create a schedule for inspections, focusing on high-wear items that may require more frequent attention. If any signs of wear or damage are detected, consider replacing the affected components promptly to ensure continued functionality and safety.
Guide to Finding Replacement Components
When it comes to maintaining outdoor power equipment, ensuring that you have access to the necessary components is essential for optimal performance. Whether you’re looking to replace a worn-out element or upgrade your tool, understanding how to find the right substitutes can save you time and effort. This section provides valuable insights into locating suitable replacements for your equipment.
The first step in the search for suitable components is to identify the specific requirements of your equipment. This includes understanding the model and specifications, which will help narrow down your options. Consulting the user manual or product documentation can provide useful information regarding compatible alternatives.
Once you have a clear idea of the required specifications, consider exploring various sources. Authorized retailers, local hardware stores, and online marketplaces are excellent places to begin your search. Be sure to check customer reviews and product ratings to ensure the reliability of the components you are considering.
Additionally, engaging with online forums or communities dedicated to outdoor equipment can provide helpful recommendations. Fellow users often share their experiences and can guide you toward reputable suppliers or compatible components that may not be widely advertised.
Lastly, if you encounter difficulties in finding the right substitutes, do not hesitate to reach out to customer support from the manufacturer. They can offer insights and guidance on sourcing the appropriate components for your specific needs. With these strategies, you can confidently locate the necessary items to keep your equipment functioning smoothly.
Importance of Proper Chain Alignment
Ensuring that the cutting mechanism is correctly aligned is crucial for optimal performance and safety. Proper alignment minimizes wear on the components and enhances efficiency during operation. Misalignment can lead to increased friction, causing the device to work harder and potentially resulting in premature failure.
Accurate positioning not only improves cutting precision but also reduces the risk of kickback, a dangerous situation where the cutting tool unexpectedly jerks backward toward the operator. This highlights the necessity of regular checks and adjustments to maintain alignment.
Additionally, maintaining correct chain alignment contributes to the overall longevity of the equipment. Components that are in sync operate smoothly, leading to less strain and maintenance over time. In essence, prioritizing proper alignment is a fundamental practice that can significantly impact performance and safety.
How to Lubricate Chainsaw Mechanisms
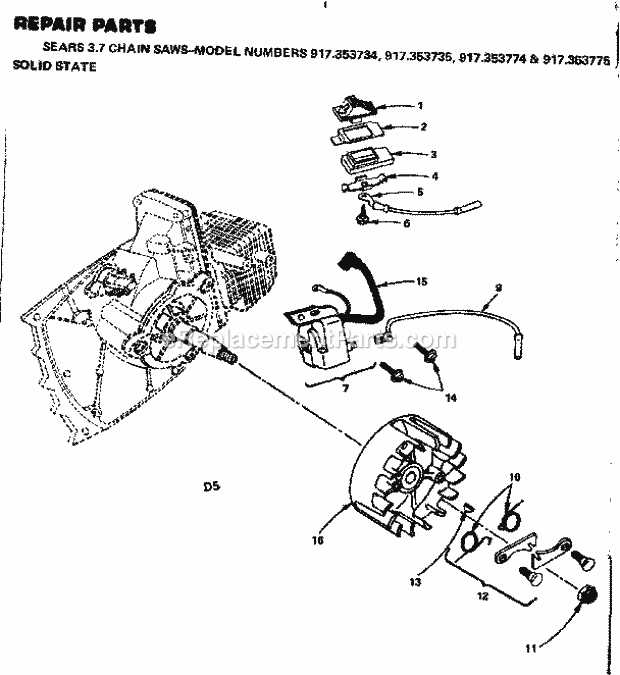
Proper maintenance of cutting tools involves ensuring that all moving components are well-lubricated. Adequate lubrication reduces friction, minimizes wear, and enhances the overall efficiency of the tool. By understanding how to effectively apply lubricant, users can prolong the lifespan of their equipment and ensure optimal performance during operation.
To begin, select a high-quality lubricant specifically designed for mechanical systems. It is crucial to avoid using unsuitable substances that may degrade the internal mechanisms. Before applying any lubricant, ensure that the tool is turned off and disconnected from any power source to prevent accidents.
Next, locate the lubrication points, which are typically indicated in the user manual. Apply the lubricant sparingly to these areas, allowing it to penetrate and coat the moving parts. Make sure to wipe away any excess to prevent accumulation of debris that could hinder performance. Regularly inspecting and reapplying lubricant as needed is essential to maintain smooth operation.
Lastly, after lubricating the mechanisms, run the tool briefly to distribute the lubricant evenly. This practice ensures that all components are adequately coated, providing protection against wear and tear during subsequent use. Regular maintenance routines, including lubrication, will significantly enhance the durability and efficiency of your cutting tool.