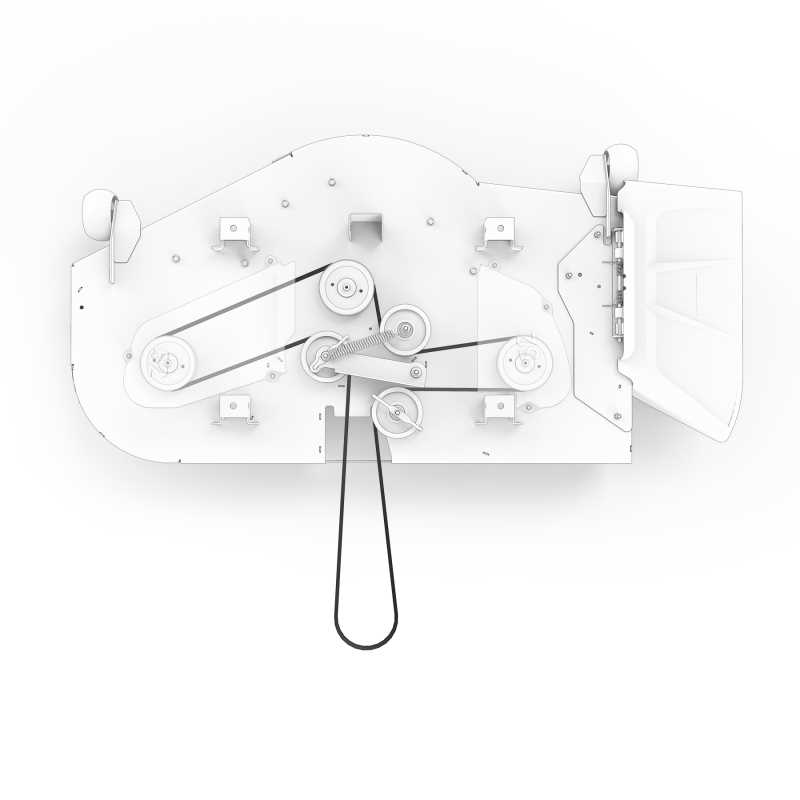
Understanding the different elements that make up a machine is crucial for efficient operation and maintenance. Each component plays a vital role in ensuring the equipment functions smoothly, and recognizing how these parts fit together can aid in troubleshooting and repairs.
This section delves into the various mechanical elements of the equipment, highlighting the essential aspects of its construction. By breaking down the main features, it becomes easier to grasp the functionality and interconnections of the system’s core elements.
In the following text, we’ll explore the structure of the machine and discuss how different sections work together, providing clarity on the mechanical design.
Key Components Overview
The system is made up of essential elements that ensure its reliable and efficient operation. Each component plays a crucial role in the overall functionality, providing both stability and precision in performance.
Engine and Transmission
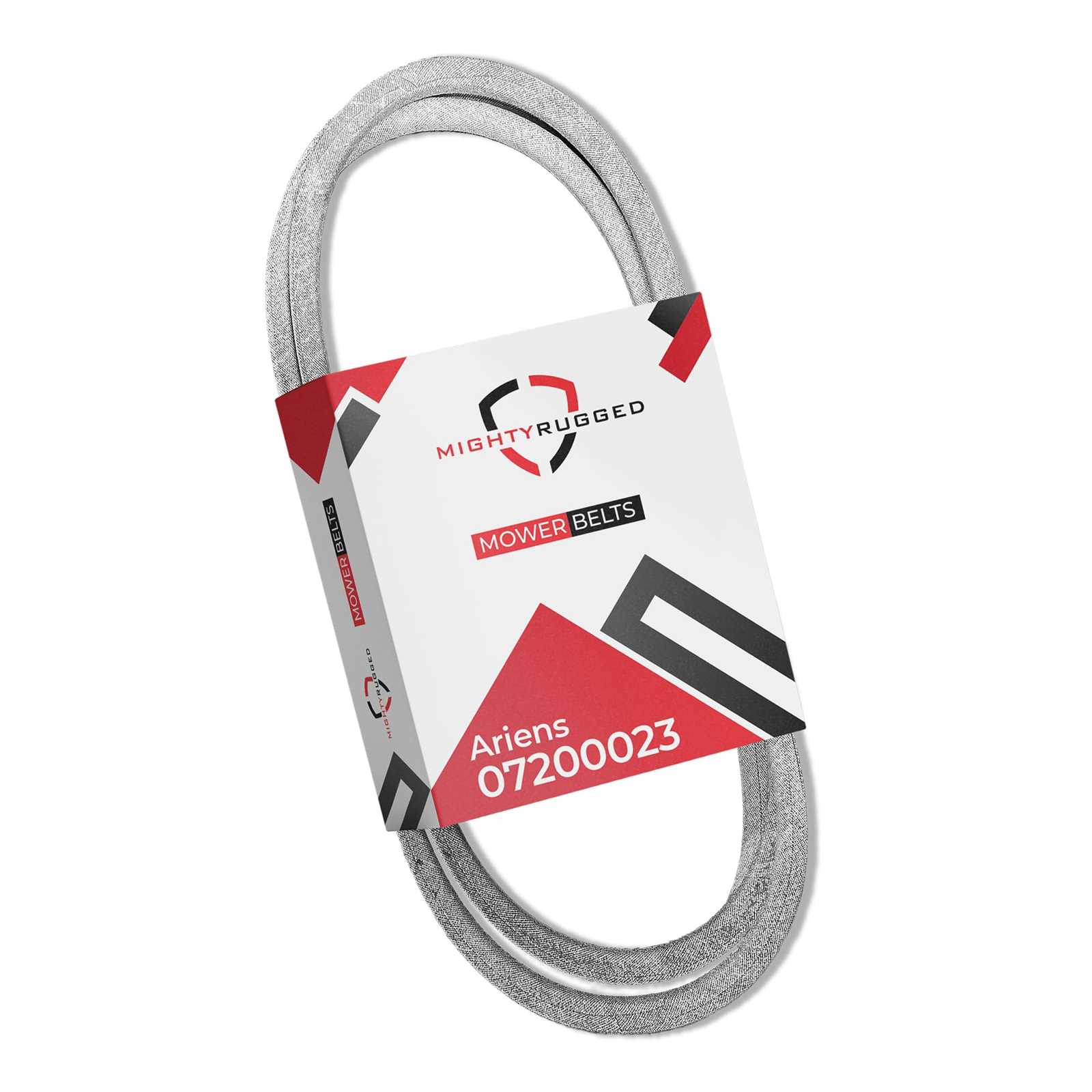
- The power unit delivers consistent force, allowing the system to tackle various tasks with ease.
- The transmission mechanism ensures smooth transitions, providing controlled movement across different terrains.
Control Mechanisms
- Steering system allows for precise direction changes, enabling smooth maneuvering.
- The adjustable settings offer customization, ensuring comfort and ease of use during operation.
Engine Specifications and Maintenance Guide
Understanding the key characteristics of your engine is crucial for ensuring its long-term performance and reliability. This guide provides an overview of the most important specifications and tips on maintaining optimal functionality without needing constant repairs.
Core Engine Specifications
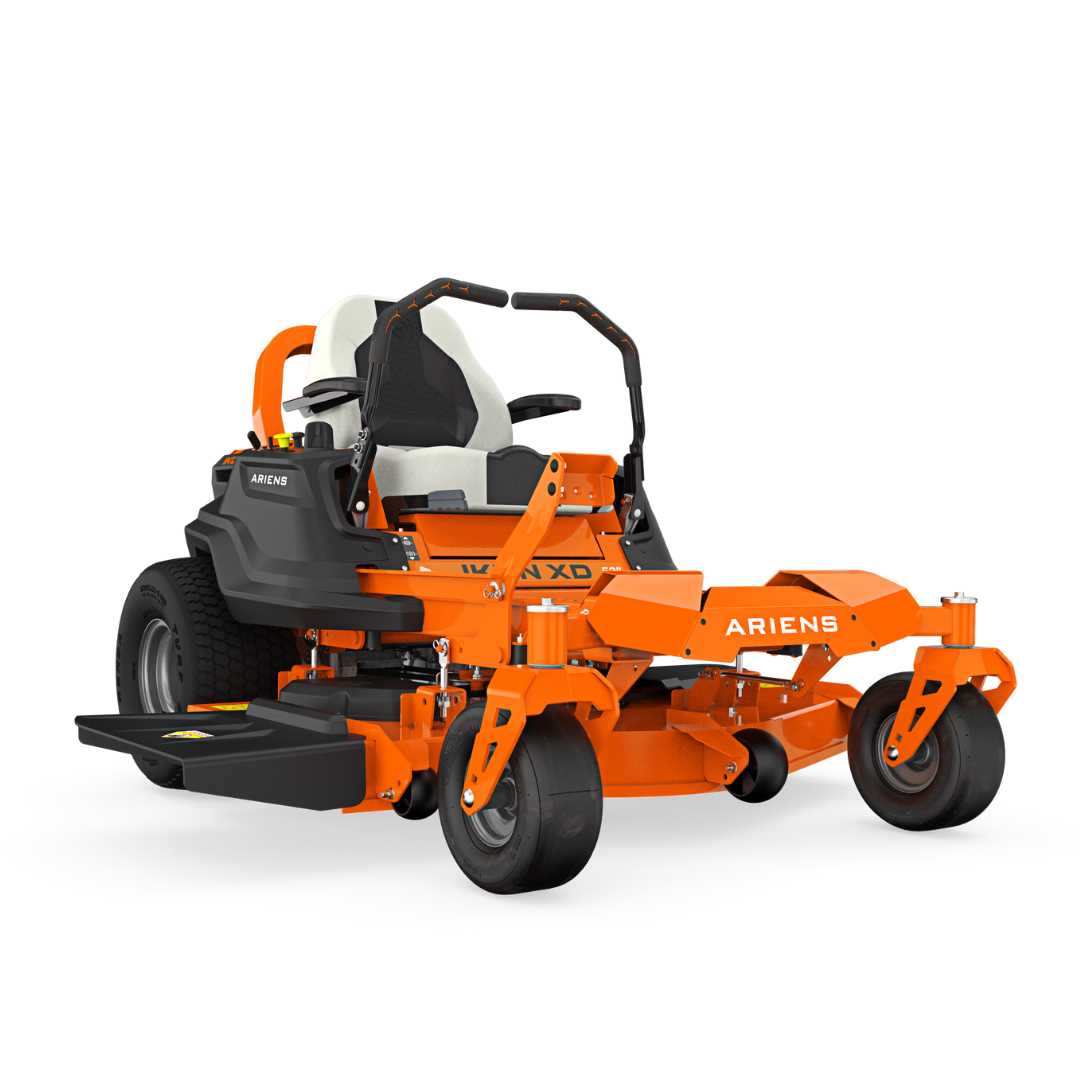
The engine’s power output, fuel efficiency, and cooling system are all factors that contribute to its overall performance. It’s important to familiarize yourself with these features to better understand how your equipment operates under various conditions. Regular monitoring of fuel levels, oil type, and temperature controls can help extend the life of the engine.
Maintenance Recommendations
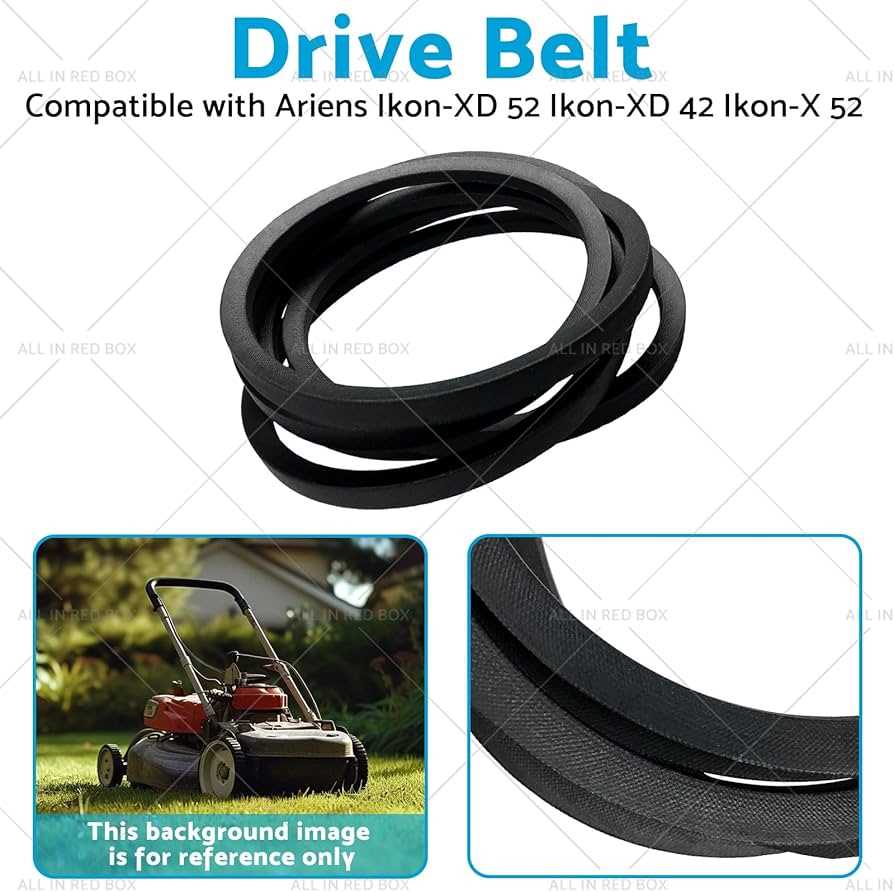
Consistent care of the engine is necessary to keep it functioning at peak performance. This includes regular oil changes, inspecting air filters, and checking for any potential leaks or worn components. Maintaining proper lubrication and replacing essential fluids at recommended intervals can prevent mechanical failures and ensure smooth operation over time.
Mower Deck Structure and Functions
The mower deck plays a critical role in ensuring efficient grass cutting, housing essential components that work together to deliver optimal performance. Understanding its construction and how it operates helps users maintain the system for longer-lasting functionality.
Main Components of the Mower Deck
The deck is made up of several important parts, including the blades, spindles, and belts, which collaborate to cut grass evenly. The frame supports these elements and is designed to handle the vibrations and stress that occur during mowing.
How the Deck Contributes to Cutting Efficiency
The position and angle of the blades directly affect the quality of the cut. The deck’s design ensures proper airflow, which lifts the grass for a precise cut, while the rotation of the blades allows for quick and efficient trimming. The belt system provides power to the blades, keeping the operation smooth.
Component |
Function |
Blades |
Responsible for cutting the grass at an even height. |
Spindles |
Connect the blades to the deck and allow rotation. |
Belts |
Transfer power from the engine to the blades. |
Drive System and Transmission Layout
The drive system and transmission are key components that ensure smooth operation and optimal performance. Understanding how these systems interact provides insight into how the machine moves efficiently across different surfaces and handles various terrains.
- The drive mechanism transfers power from the engine to the wheels, allowing for controlled movement.
- The transmission regulates speed and torque, adapting to the needs of the operator and environmental conditions.
- Proper alignment and maintenance of these systems can enhance durability and reduce wear over time.
Overall, a well-maintained drive and transmission system not only improves the machine’s performance but also ensures longevity and reliability during extended use.
Blade Mechanism and Replacement Tips
The blade system plays a crucial role in the efficiency and overall performance of the equipment. It ensures smooth and precise cutting while operating, and regular maintenance is essential to keep it functioning optimally. Understanding the operation of this mechanism and knowing when and how to replace the blades can significantly extend the lifespan of the device.
Understanding the Blade System
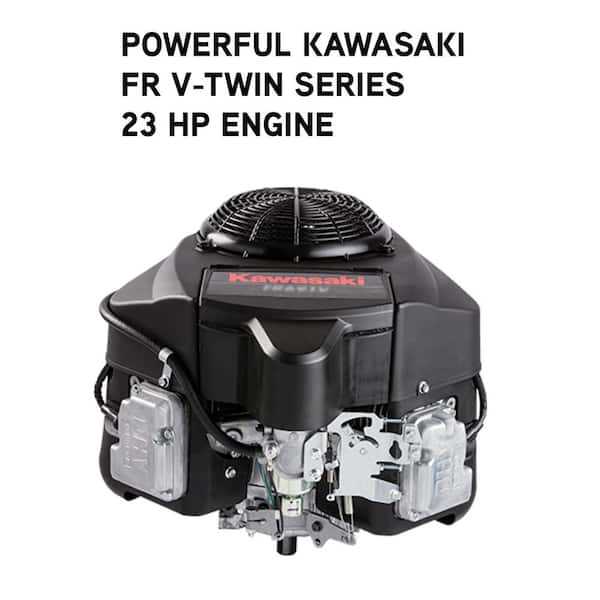
The cutting blades are connected to a rotating shaft, which is powered by the engine. The rotation speed and angle determine the quality of the cut, and any wear or damage can affect performance. It’s important to monitor the sharpness and condition of the blades to ensure consistent cutting results.
Steps for Replacing Blades
Step |
Description |
1 |
Disconnect the power source to ensure safety during the process. |
2 |
Locate the blade assembly and use the appropriate tools to loosen the bolts securing the blades. |
3 |
Remove the old blades, inspect the shaft and other parts for wear, and clean the area if necessary. |
4 |
Install new blades, ensuring they are properly aligned and securely fastened. |
5 |
Steering and Control Features Explained
Understanding the steering and control mechanisms is crucial for ensuring smooth operation and maneuverability. These features allow for precise handling, making navigation easy and efficient even in tight spaces or on uneven terrain.
- Responsive Steering: The system offers swift reactions to directional inputs, allowing for smooth transitions and minimal effort while turning.
- Enhanced Stability: Stability controls ensure the machine remains balanced and steady, reducing the risk of tipping or loss of control during operation.
- Effortless Maneuvering: Thanks to advanced control settings, users can easily navigate different terrains without experiencing strain or difficulty in adjusting speed and direction.
- Customizable Controls: Settings can be fine-tuned to suit individual preferences, offering a more comfortable and tailored experience for operators of all skill levels.
Fuel and Electrical System Layout
The configuration of the fuel and electrical systems is crucial for the optimal performance of the machinery. This layout encompasses various components that work in harmony to ensure efficient operation, reliability, and safety. A clear understanding of these systems is essential for maintenance and troubleshooting, as it aids in identifying potential issues and streamlining repairs.
The fuel system typically includes elements such as the fuel tank, lines, filters, and the carburetor, each playing a vital role in delivering the correct amount of fuel to the engine. Proper routing and connections are necessary to prevent leaks and ensure smooth fuel flow.
In parallel, the electrical system comprises the battery, ignition components, wiring harnesses, and various sensors. This network provides the necessary power for starting the engine and operates essential accessories. Ensuring that all connections are secure and that components are in good working order is key to preventing electrical failures.
In summary, a comprehensive overview of the fuel and electrical systems provides insight into their respective functions and interconnections, facilitating effective maintenance and enhancing the overall performance of the equipment.
Cutting Performance and Height Adjustment
The efficiency of a cutting tool greatly depends on its ability to adapt to various grass heights and conditions. A well-designed mechanism allows for precise adjustments, ensuring optimal performance during use. This flexibility enhances the overall cutting experience, enabling users to achieve a clean and uniform finish.
Factors Influencing Cutting Efficiency
- Blade Sharpness: Regular maintenance of blade sharpness is crucial for achieving a clean cut and preventing damage to the grass.
- Cutting Speed: The speed at which the tool operates can affect the quality of the cut. Finding the right balance is essential for optimal results.
- Grass Conditions: Understanding how different types of grass react to cutting can help in adjusting techniques accordingly.
Height Adjustment Mechanism
- Manual Adjustment: Many devices feature a simple lever or dial for height modification, allowing users to quickly adapt to changing conditions.
- Automatic Systems: Some advanced models come equipped with sensors that automatically adjust the cutting height based on the terrain.
- Height Indicators: Clear indicators help users to set the desired height accurately, ensuring consistent cutting performance.
Safety Mechanisms and Protective Features
Effective safety systems and protective elements are essential in modern machinery to ensure user security and prevent accidents during operation. These features are designed to mitigate risks and enhance the overall safety of equipment, providing users with peace of mind while operating the device.
Key Safety Mechanisms
- Emergency Stop Switch: A crucial component that allows operators to quickly halt machinery in case of an emergency, preventing potential injuries.
- Operator Presence Control: This feature requires the operator to maintain a certain position, ensuring that the machine will not operate if they are not present, reducing the risk of unintended activation.
- Safety Guards: Physical barriers that protect users from moving parts, minimizing the likelihood of accidents.
Protective Features
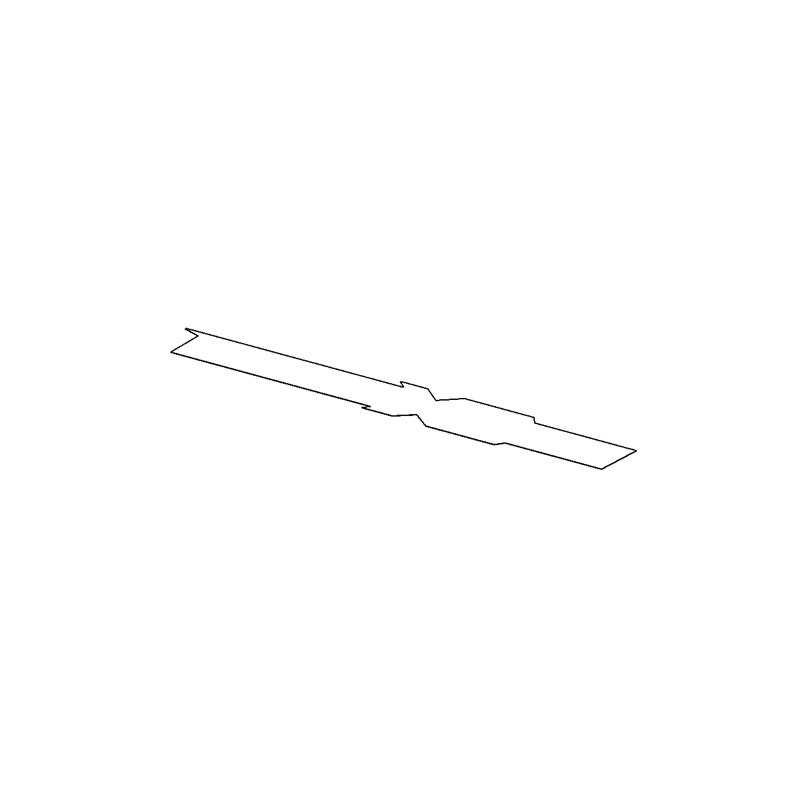
- Anti-rollback Systems: These systems help prevent the machine from rolling backward on inclines, enhancing stability and user control.
- Overload Protection: Sensors that detect excessive load conditions, automatically shutting down the equipment to prevent damage and enhance user safety.
- Noise Reduction Technologies: Features that minimize operational noise, contributing to a safer working environment by reducing auditory strain on operators.