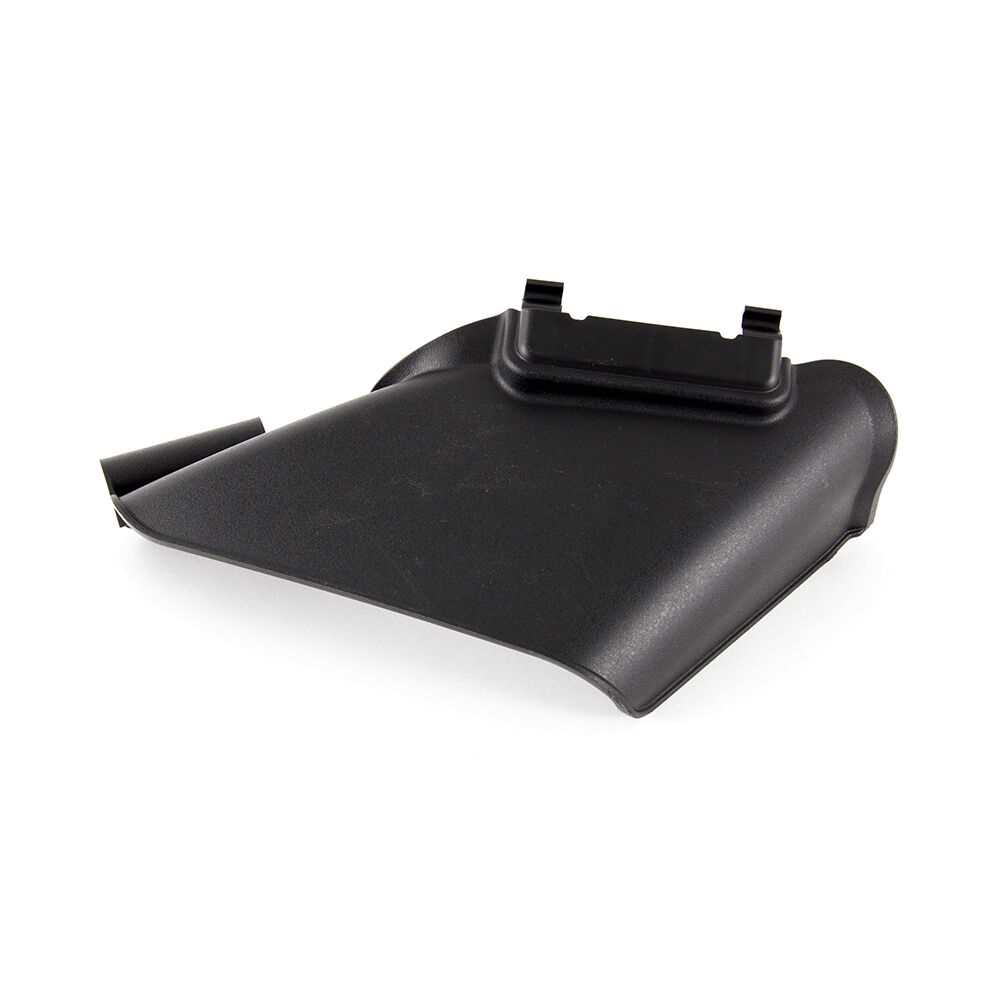
When working with a complex mechanical device, it is essential to have a clear understanding of how each element fits into the overall system. Knowing the structure and roles of individual elements can help in maintaining and optimizing the performance of the equipment.
In this guide, we will explore the different mechanical elements of the machine, detailing their roles and importance. By getting familiar with these essential pieces, you will be better equipped to handle maintenance tasks and ensure the smooth operation of your equipment.
Each component plays a critical role, working in harmony with the others to deliver efficient performance. Let’s take a closer look at the various elements and how they contribute to the overall functionality of the system.
12avb2a3711 Parts Diagram Overview
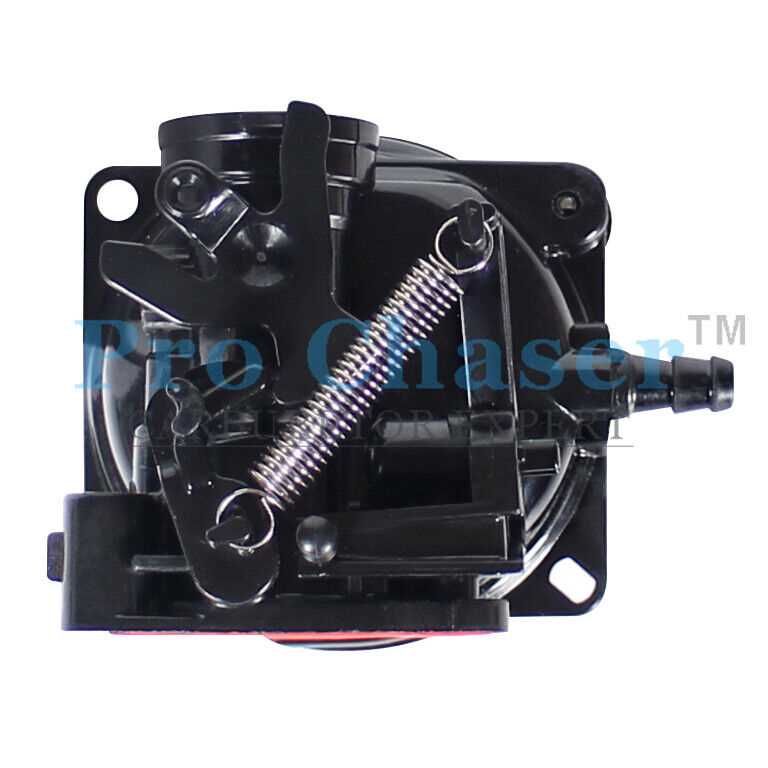
Understanding the layout and structure of various components is crucial for efficient maintenance and troubleshooting. This section provides a detailed view of the assembly, helping users identify key elements and their placement within the system. The arrangement allows for a clear understanding of how different segments connect and function together.
Key components are highlighted to ensure easy recognition, while interconnected elements are carefully explained to demonstrate their roles within the overall structure. This visual representation simplifies the process of locating specific units and understanding their purpose within the machine.
Key Components of 12avb2a3711
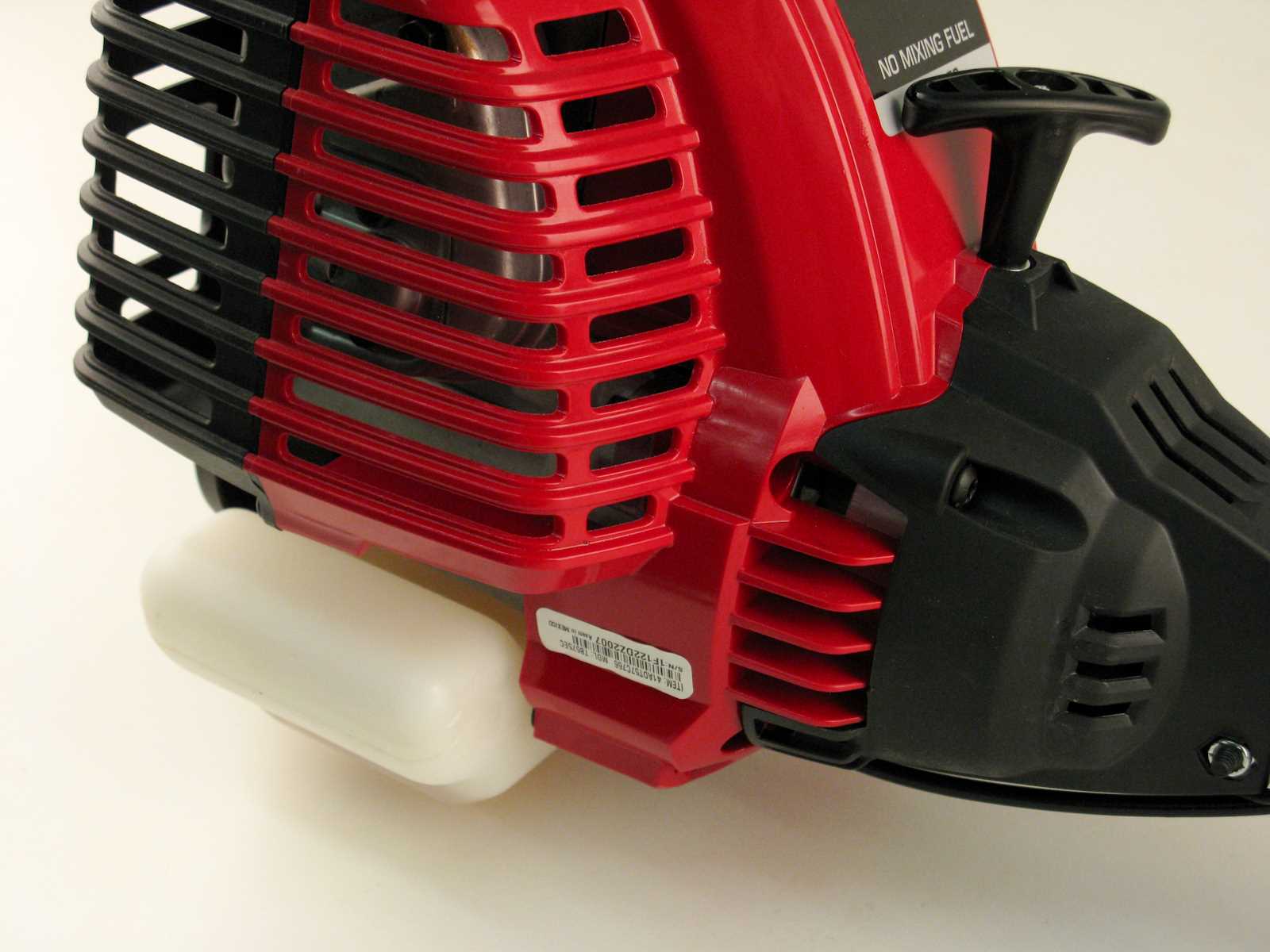
The structure consists of several essential elements that work together to ensure optimal functionality. These elements are strategically placed to provide efficiency and reliability during operation. Understanding the primary components allows for better maintenance and improved performance over time.
Engine: The core of the system, this unit provides the necessary power for movement. Its design ensures a balance between strength and fuel efficiency, allowing for smooth and consistent operation.
Blades: Positioned at the bottom, these sharp-edged elements are responsible for cutting. Their durability and sharpness contribute to achieving precise and clean results.
Drive System: This mechanism connects the power source to the wheels, ensuring movement. The system’s smooth operation allows for controlled movement over various terrains.
Wheels: Designed for stability, the wheels offer strong traction and durability. Their size and design contribute to maneuverability, allowing easy handling on different surfaces.
Handle: This component provides the user with control. Its ergonomic design ensures comfort during extended use, reducing strain and enhancing the overall user experience.
Detailed Breakdown of the Engine Section
The engine section is a critical component, requiring a thorough understanding of its individual elements to ensure proper functionality. By examining each part, we can better understand how the entire system works together to deliver optimal performance. This section provides an in-depth exploration of the main areas, highlighting the key components and their roles in the overall operation.
Component |
Function |
Cylinder |
Houses the pistons and supports combustion for power generation. |
Piston |
Moves within the cylinder to convert combustion pressure into mechanical motion. |
Crankshaft |
Transforms the piston’s linear motion into rotational energy. |
Valves |
Regulate the intake of air and fuel as well as the release of exhaust gases. |
Spark Plug |
Exploring the Transmission Assembly
The transmission system is a crucial component that ensures the proper transfer of power from the engine to the wheels. Understanding how this mechanism works can offer insights into the overall efficiency and performance of the machinery. This section will provide a detailed look into its key components and their functions, helping to appreciate the complexity of this essential system.
Main Components of the Transmission
- Clutch: The clutch serves as a connection point between the engine and transmission, allowing for smooth engagement and disengagement of power.
- Gearbox: The gearbox adjusts the speed and torque, enabling the machine to operate under various conditions with optimal efficiency.
- Driveshaft: This component transmits the mechanical power to the wheels, ensuring effective movement and control.
How the System Operates
- Power Flow: The engine generates power, which passes through the clutch and gearbox before reaching the driveshaft.
- Gear Shifting: The gearbox allows for changes in speed by
Understanding the Blade and Deck Mechanism
The blade and deck system plays a crucial role in ensuring efficient performance. This section focuses on explaining how these components work together to achieve a smooth operation. By understanding their interaction, you’ll gain insights into maintaining and improving their functionality.
The Role of the Blade
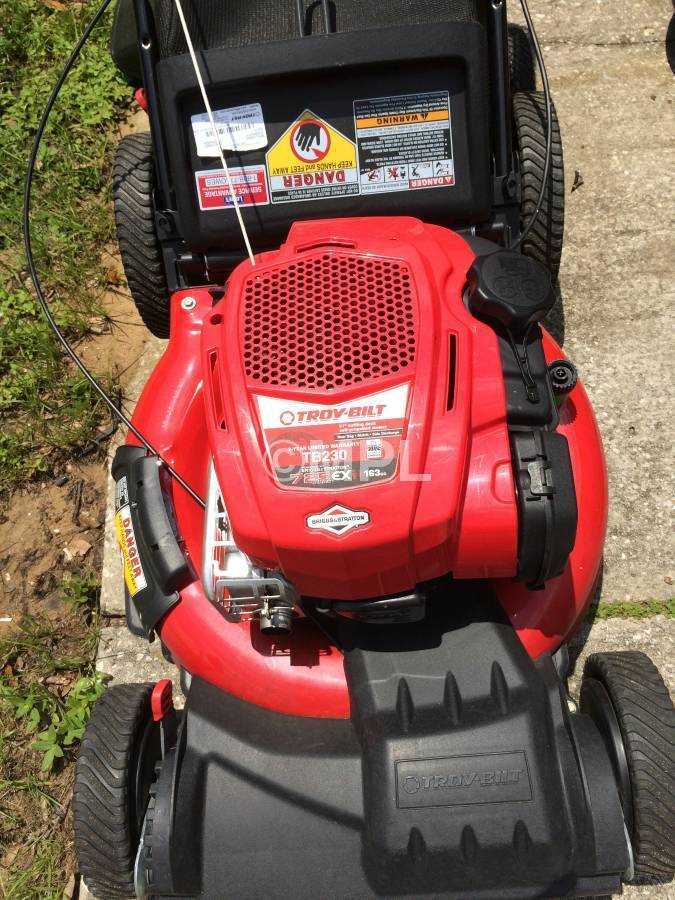
The blade is responsible for cutting and mulching. Its design and sharpness impact the quality of the cut and overall efficiency. Keeping the blade in top condition ensures a cleaner and more precise result, reducing the need for repeated passes.
The Functionality of the Deck
The deck houses the blade and controls how the grass is processed. It determines the airflow and helps direct the clippings. The deck’s height can often be adjusted to accommodate different grass lengths, allowing for flexibility in various mowing conditions.
- Blade sharpness affects cut quality and performance.
- Deck design impacts airflow and clippings direction.
- Height adjustments ensure adaptability for different grass lengths.
Electrical System Layout and Features
The arrangement and characteristics of the electrical framework play a vital role in ensuring optimal functionality and efficiency. This segment delves into the intricacies of how the electrical components are organized, highlighting their interconnections and operational capabilities.
Configuration of the Electrical Components
Understanding the configuration of electrical elements is essential for troubleshooting and maintenance. The layout typically includes various devices such as switches, circuits, and connectors, all strategically placed to enhance performance. Each component interacts with others, creating a cohesive network that facilitates energy flow and control.
Key Characteristics and Advantages
The electrical system is designed with several notable features that contribute to its reliability. Durability and efficiency are paramount, ensuring that the system can withstand various operational demands while minimizing energy losses. Additionally, safety measures are integrated into the design to protect users and equipment from potential hazards.
Maintenance Guide for 12avb2a3711 Parts
Proper upkeep of equipment components is essential for optimal performance and longevity. Understanding how to maintain these elements ensures efficient operation and prevents unexpected breakdowns. This section provides valuable insights and strategies for maintaining crucial elements, helping users extend their lifespan and functionality.
Key Maintenance Practices
- Regular Inspection: Conduct frequent checks for signs of wear or damage.
- Cleaning: Keep all components free from dust, dirt, and debris to ensure smooth operation.
- Lubrication: Apply appropriate lubricants to moving parts to reduce friction and prevent overheating.
- Calibration: Ensure that all settings are accurate and within manufacturer specifications.
Common Issues and Solutions
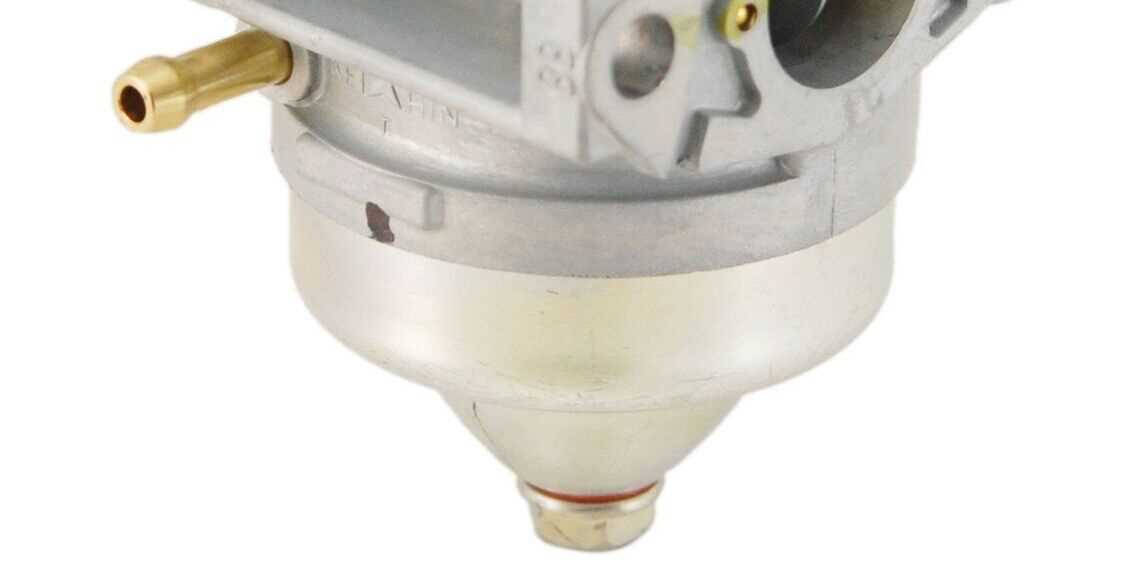
- Overheating: Ensure proper lubrication and check for obstructions that may block airflow.
- Unusual Noises: Inspect for loose parts and tighten as necessary.
- Inconsistent Performance: Verify calibration and replace worn components.
Troubleshooting Common Part Issues
When working with mechanical systems, various components may encounter problems that affect overall performance. Identifying and addressing these issues is crucial for maintaining efficiency and preventing further complications. Understanding typical faults can help users pinpoint the root causes and implement effective solutions.
Common challenges often arise from wear and tear, improper installation, or external factors like environmental conditions. Users may experience symptoms such as unusual noises, vibrations, or diminished functionality. To diagnose these issues, it is essential to perform a systematic examination of the affected components.
Start by inspecting for visible signs of damage or misalignment. Check for loose connections or fittings that may have come undone over time. It is also beneficial to consult maintenance logs for any previous repairs or replacements that could provide insights into recurring issues.
If problems persist after these initial checks, more in-depth testing may be required. Utilizing diagnostic tools can help identify discrepancies in performance, allowing for targeted repairs. Regular maintenance and timely interventions can significantly extend the lifespan of mechanical systems, reducing the likelihood of severe malfunctions.
Replacement and Upgrade Options
When considering alternatives for enhancing the performance of your equipment, it is crucial to explore various options available in the market. Upgrading specific components can significantly improve functionality and longevity. This section will delve into potential enhancements and replacements that can optimize your system’s efficiency and reliability.
Potential Enhancements
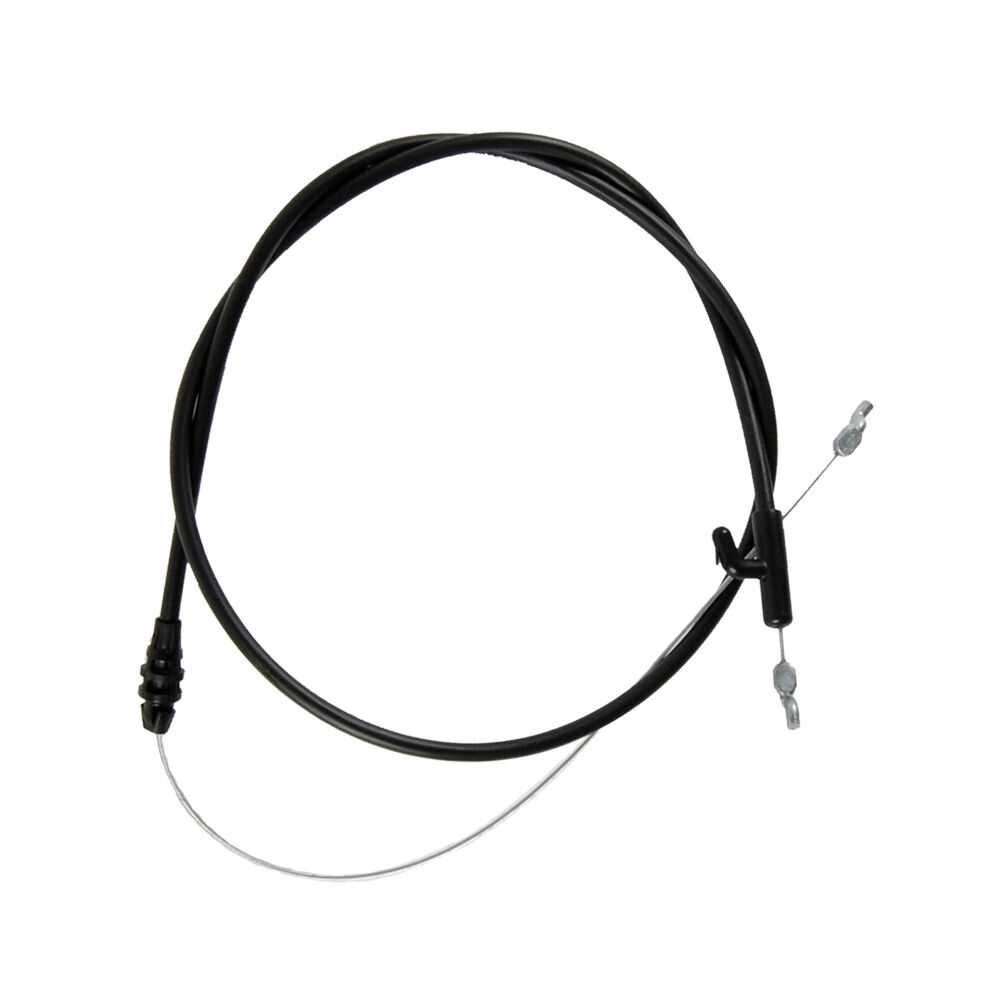
- Evaluate newer models that provide advanced features and better efficiency.
- Consider higher-grade materials that offer increased durability and performance.
- Explore custom modifications that cater to specific operational needs.
Replacement Strategies
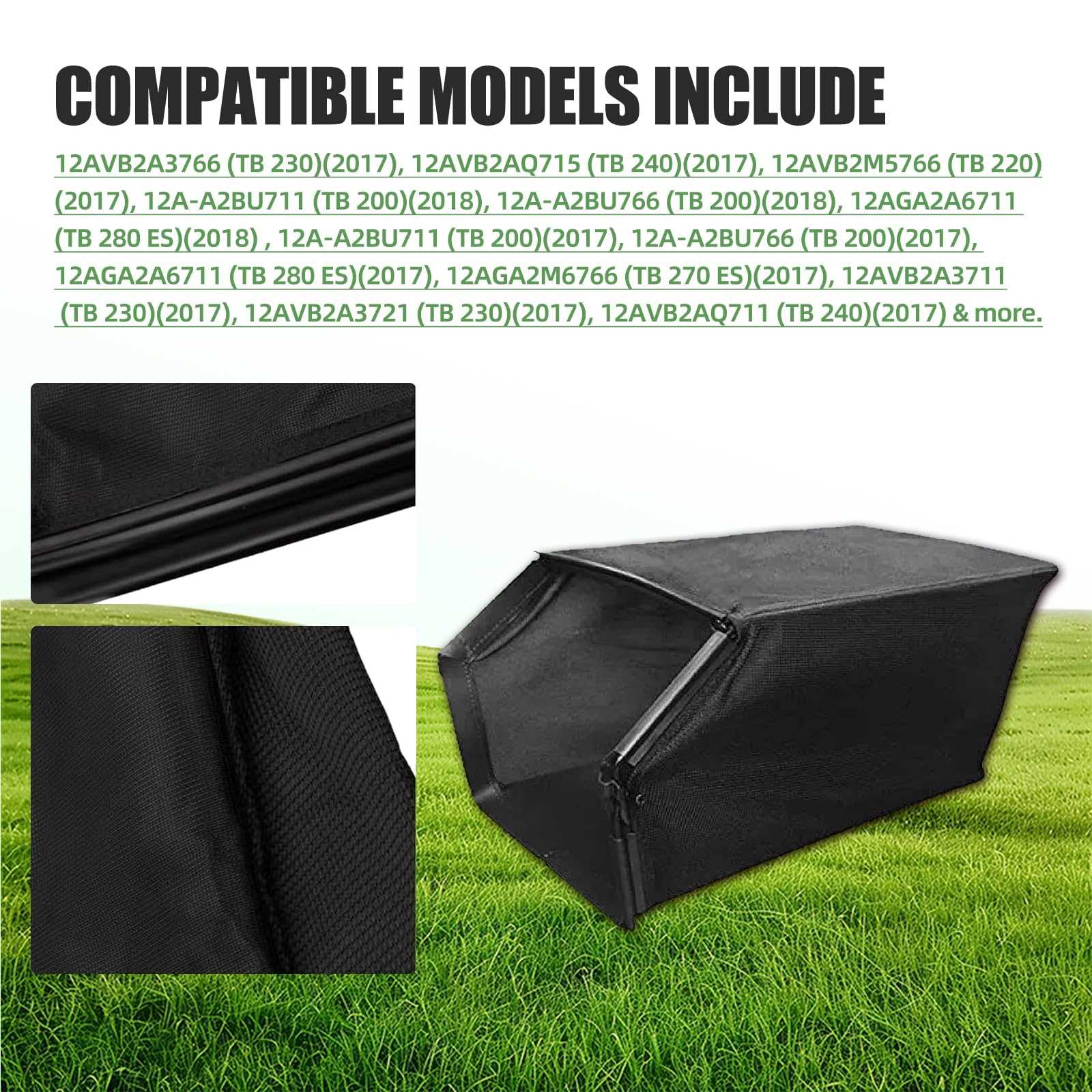
- Assess compatibility with existing systems to ensure seamless integration.
- Research user reviews and expert recommendations for quality assurance.
- Plan for future needs by selecting upgrades that allow for scalability.