Fuel
Critical Spots for Regular Maintenance
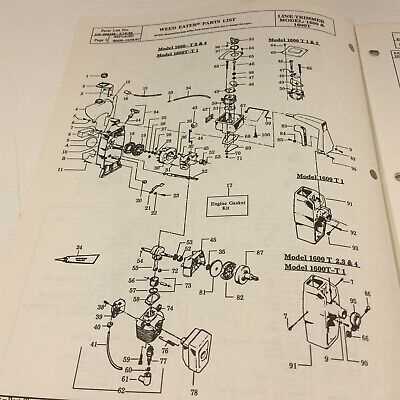
Consistent upkeep of certain mechanical components ensures smooth operation and extends the lifespan of your equipment. Focusing on key areas helps prevent unexpected breakdowns and maximizes performance over time. Below are essential areas that require regular attention to maintain functionality and efficiency.
Lubrication Points
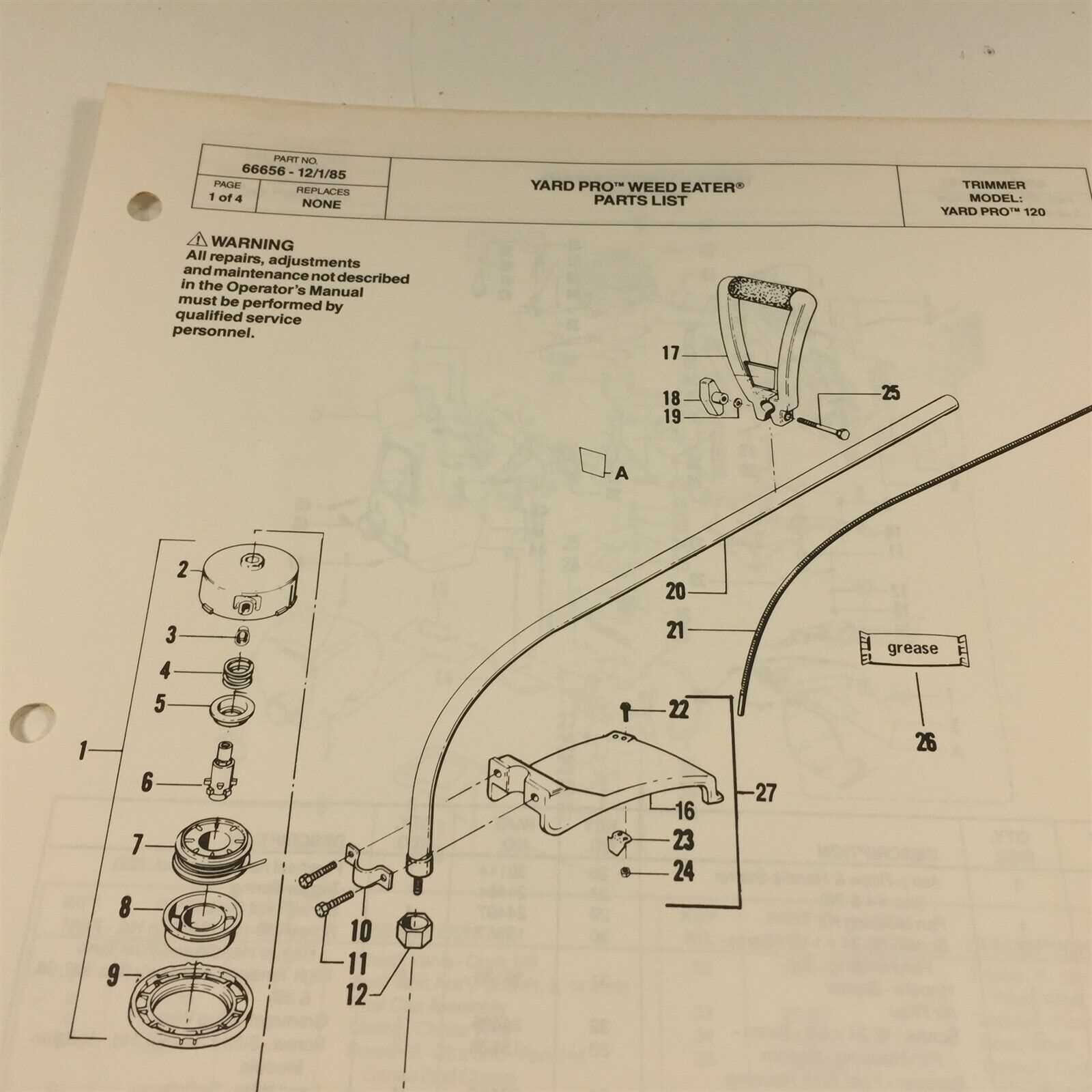
Proper lubrication is necessary for parts that undergo frequent motion or friction. These areas tend to wear out faster if left unchecked. Regularly apply suitable lubricants to moving parts, ensuring that they operate smoothly and without resistance. Inspect these points periodically for any signs of wear or dryness.
Fastening Components
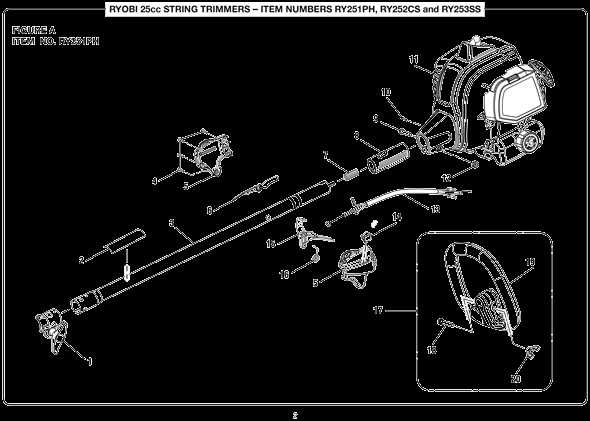
Loose screws, bolts, and other fastening elements can lead to inefficiencies or even damage if not tightened properly. Regularly inspect these connections to ensure they remain secure. Pay special attention to areas that experience significant vibration, as they are prone to loosening over time.
Component |
Maintenance Frequency |
Moving Mechanisms |
Every 10 hours of use |
Fastening Elements |
Weekly |
Lubrication Points |
Monthly |
Replacement Guide for Damaged Parts
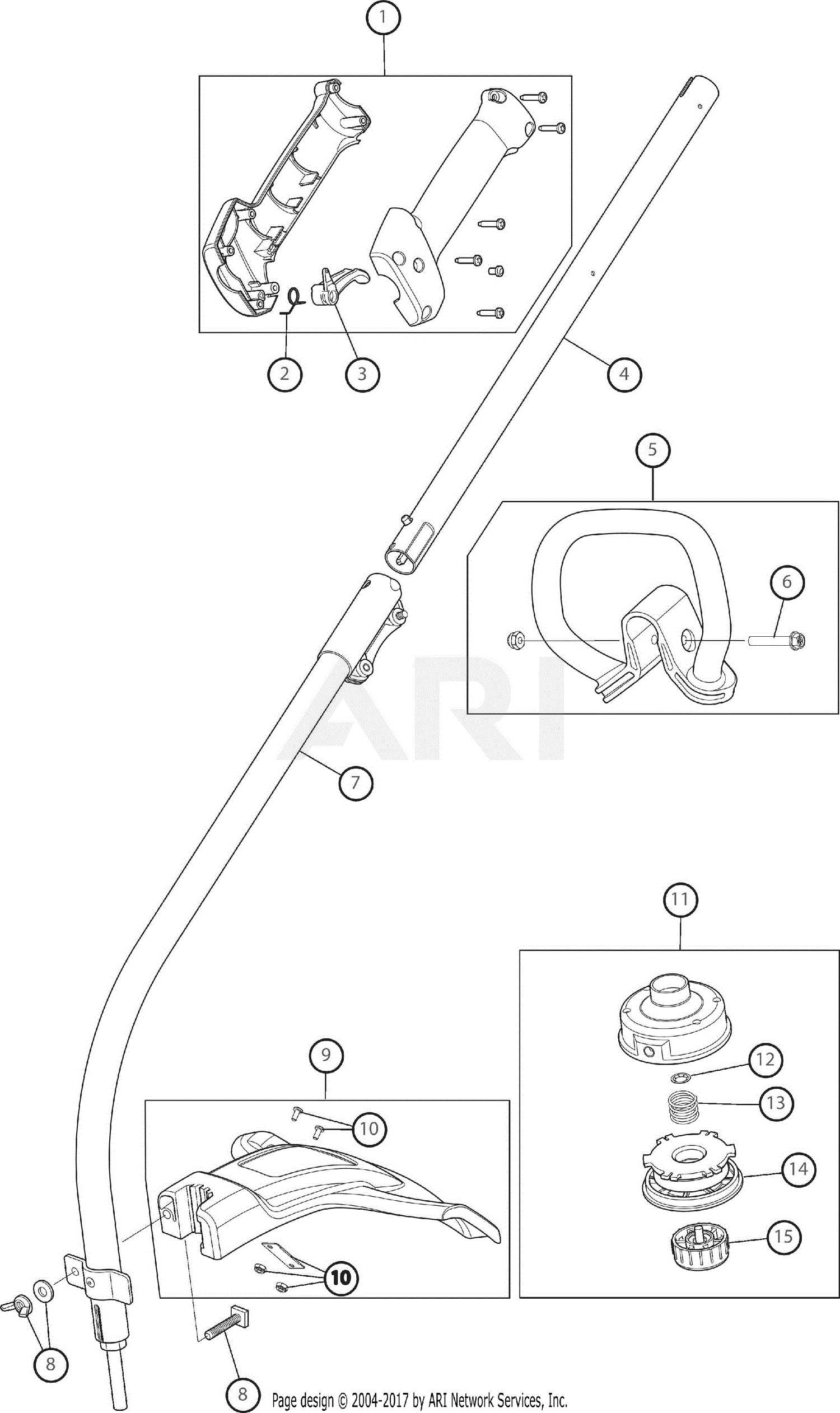
Over time, various components of outdoor tools may wear out, requiring timely attention and repair. Identifying faulty areas and replacing them with suitable alternatives ensures the tool continues to perform effectively, extending its lifespan.
Steps to Identify Faulty Components
The first step in any repair process is a thorough inspection of the device. Examine moving elements for signs of wear or malfunction, such as cracks, excessive rust, or looseness. This initial assessment helps pinpoint the areas needing attention.
Choosing Compatible Replacements
When selecting replacement elements, it’s important to match specifications precisely. Ensure the new component fits the existing design and can handle the same workload. Failure to do so could lead to inefficiencies or even further damage to the equipment.
Steps to Safely Swap Components
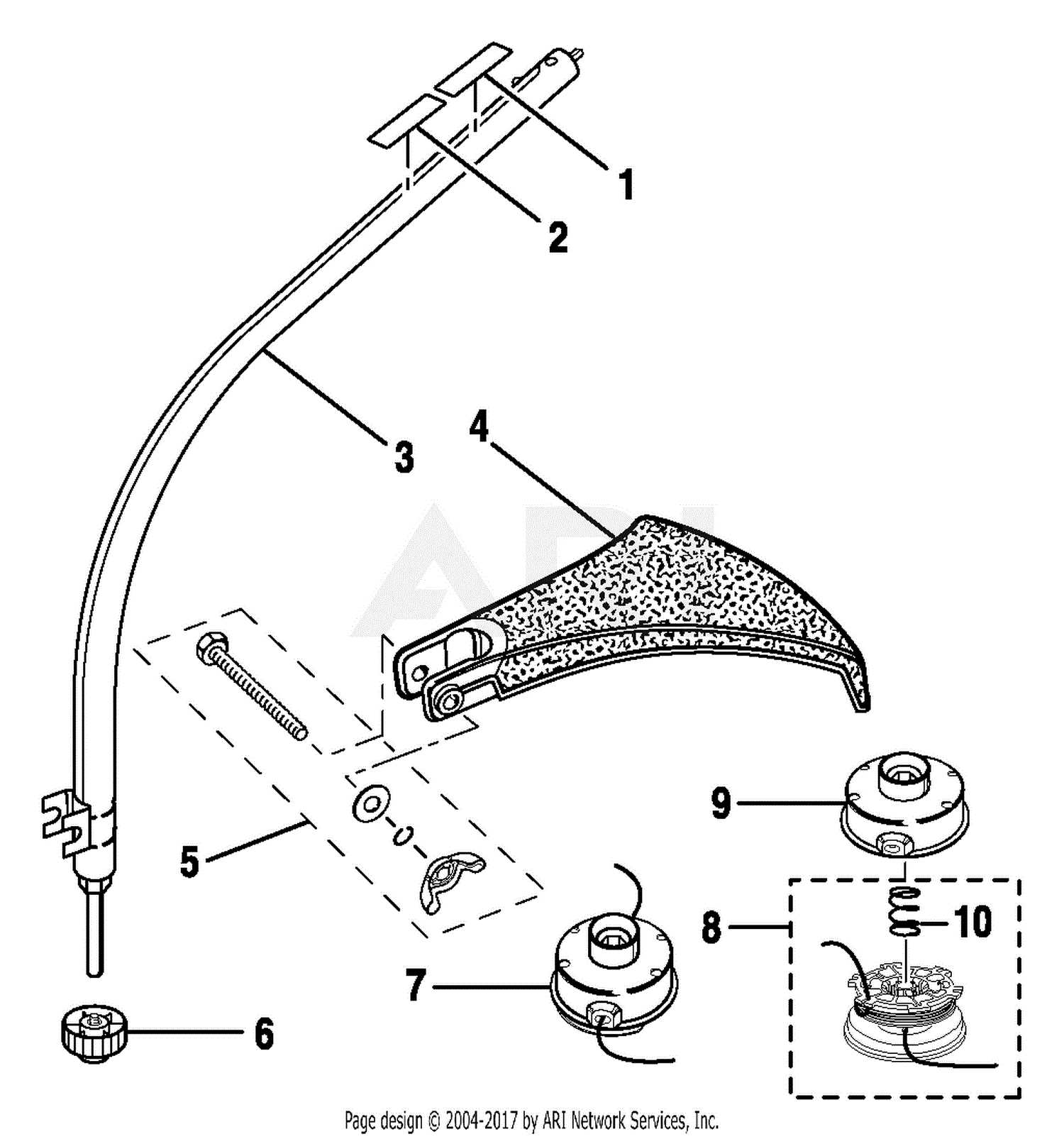
When it comes to replacing individual elements of a mechanical device, it’s crucial to follow proper procedures to ensure both personal safety and the functionality of the equipment. Careful handling and attention to detail are key to preventing damage and ensuring a smooth exchange process.
1. Disconnect Power Sources
Before beginning any work, always disconnect the tool from any power supply. This includes removing batteries, unplugging cords, or disengaging any fuel sources. Doing so ensures that no accidental starts occur during the maintenance process.
2. Inspect the Area
Examine the device closely before removing any components. Look for visible signs of wear, loose connections, or potential hazards that might interfere with the replacement. Identifying these issues early can save time and prevent mistakes during the swap.
3. Use Proper Tools
Using the correct tools for the task is essential. Make sure you have the right wrenches, screwdrivers, or other instruments needed for disassembly. Avoid improvising with inappropriate tools, as this could lead to damage or personal injury
Optimizing Performance with Correct Assemblies
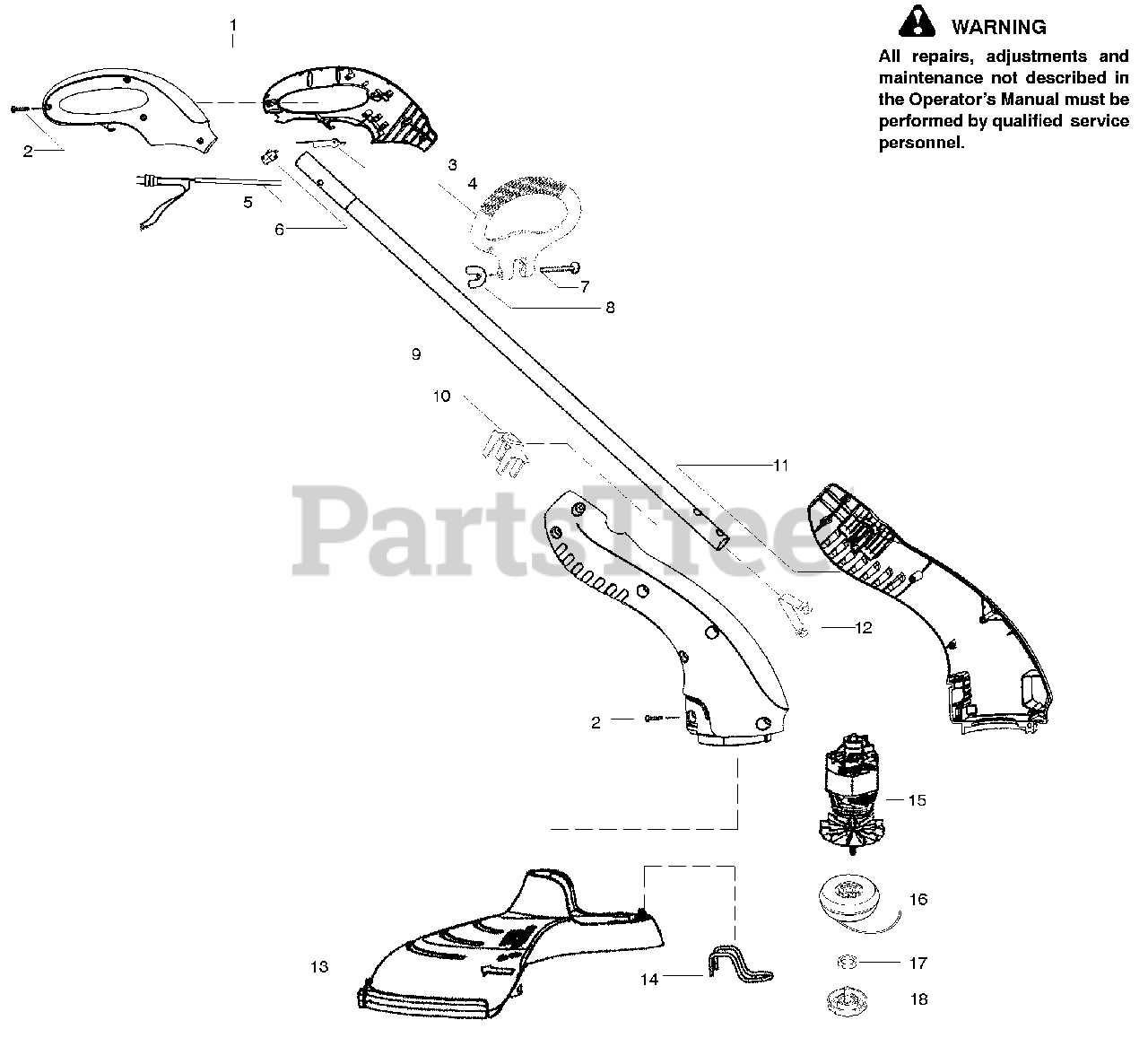
Ensuring that each element is properly aligned and installed plays a crucial role in maximizing the efficiency of any mechanical system. By focusing on precise connections and careful arrangement, the overall functionality can be significantly improved, reducing wear and extending the lifespan of the device.
Ensuring Proper Fitment
The accuracy of each component’s placement affects the machine’s smooth operation. Misaligned assemblies can lead to operational issues, such as vibrations or reduced output. Double-checking alignments and following the correct sequence during assembly ensures optimal performance and durability.
Maintaining Component Integrity
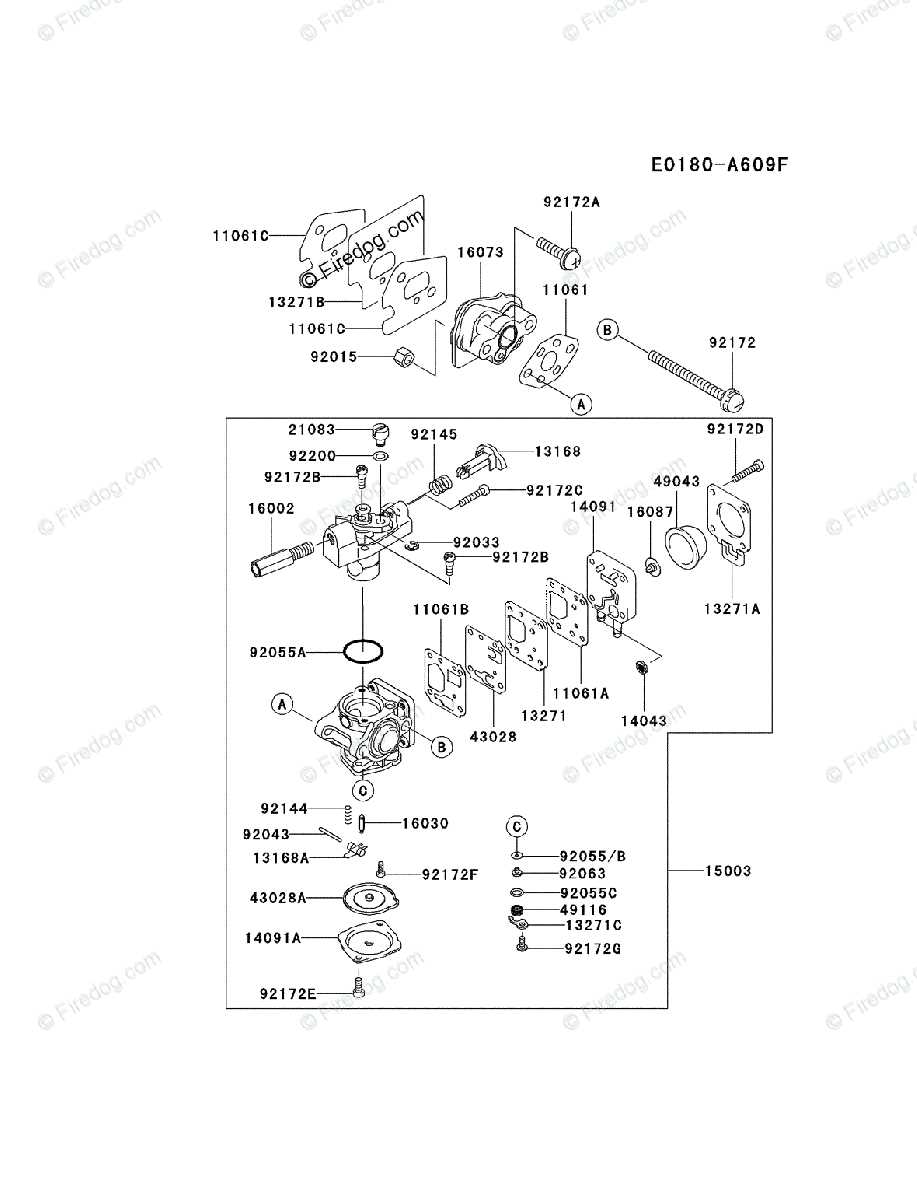
Over time, components may wear out or become damaged due to improper installation. Ensuring that every part is fitted according to the manufacturer’s recommendations helps prevent unnecessary strain, keeping the system running efficiently and reliably. Regular inspection and adjustment are essential for long-term performance.
Proper Fitting for Efficient Operation
Ensuring the correct installation of various components is crucial for smooth and effective functionality. When each element is aligned and fitted accurately, the overall performance improves significantly, leading to less strain and more reliable outcomes.
Key Considerations for Accurate Assembly
- Match the dimensions of each element to the designated slots to avoid misalignment.
- Securely fasten all connections, ensuring there are no loose fittings that could hinder performance.
- Double-check the positioning of moving parts to prevent unnecessary friction or wear.
Common Mistakes to Avoid
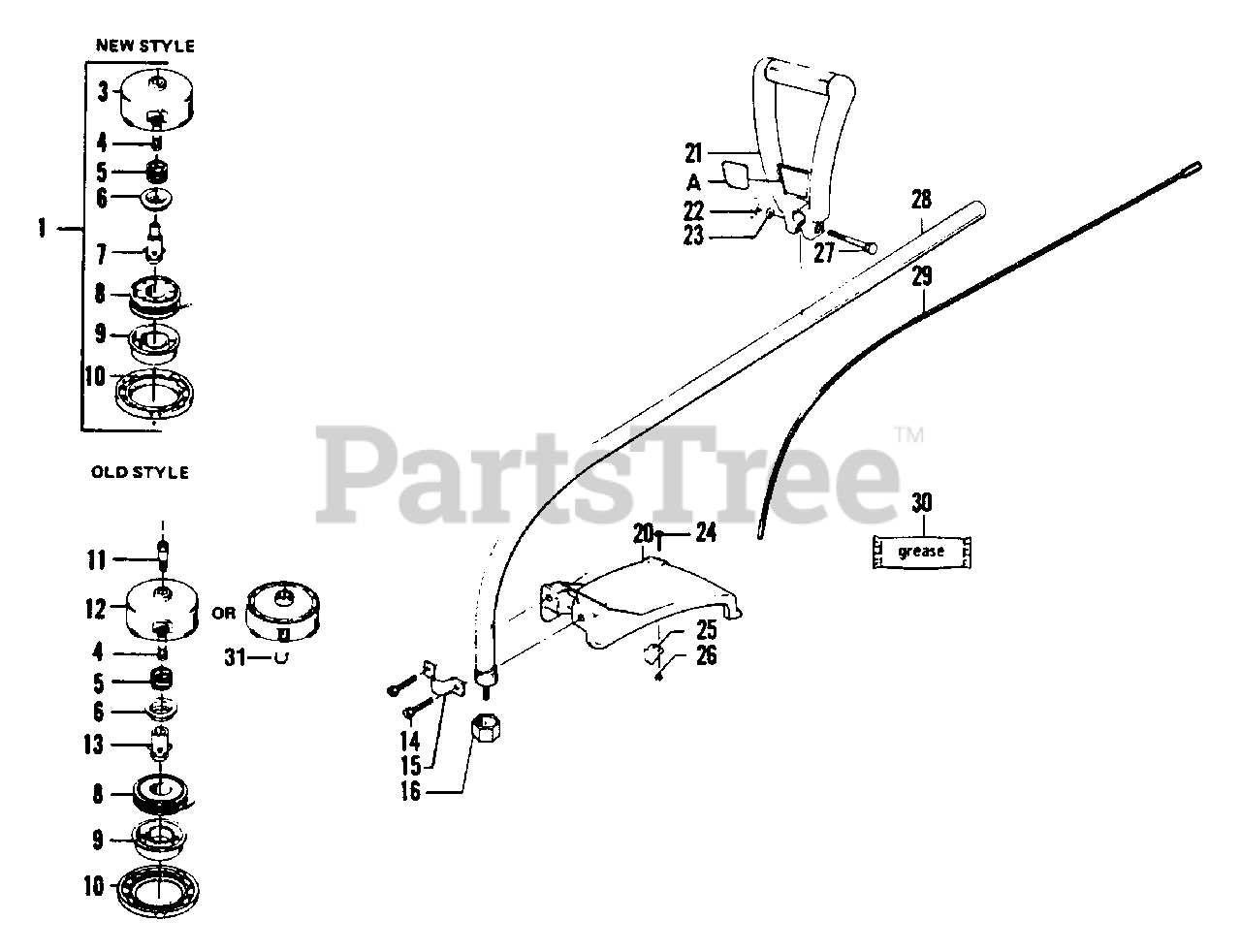
- Forcing elements into incorrect positions, leading to potential damage.
- Neglecting to tighten adjustable connections, resulting in instability during operation.
- Ignoring compatibility guidelines between various components, which may reduce efficiency.
Troubleshooting Mechanical Failures
Mechanical issues can arise in any device, impacting its performance and efficiency. Identifying the root causes of these failures is essential for effective repair and maintenance. By following a systematic approach, users can address common mechanical problems and restore functionality.
Common Mechanical Issues
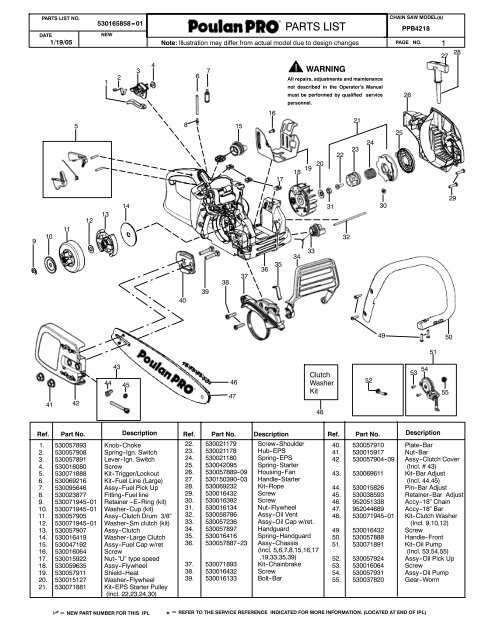
- Overheating: Excessive heat may lead to component wear and potential failure.
- Unusual Noises: Grinding or rattling sounds can indicate loose or damaged components.
- Vibration Problems: Excessive vibration often signifies misalignment or imbalance.
- Difficulty Starting: Problems with ignition or power delivery can prevent operation.
Steps for Diagnosis
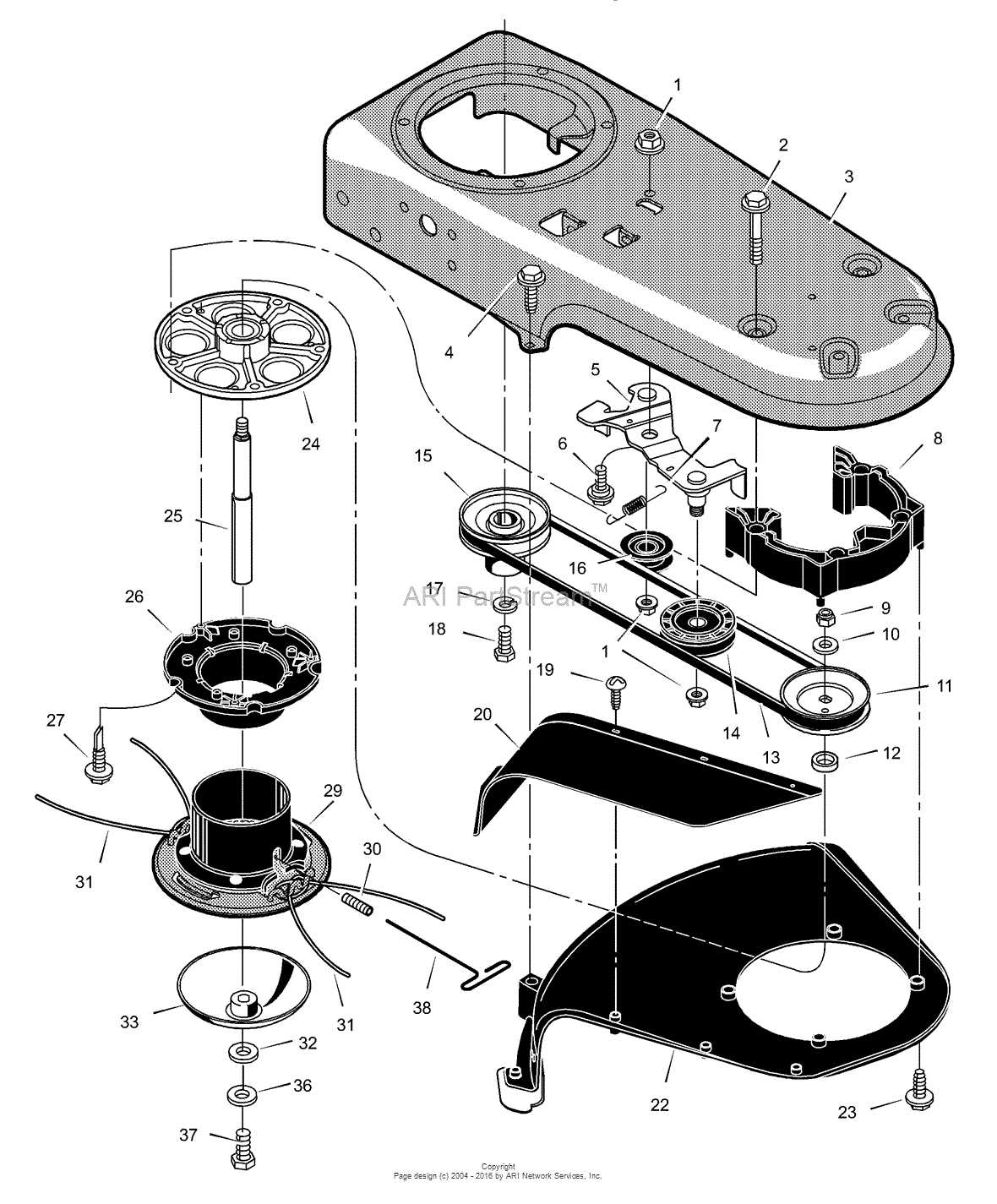
- Inspect the device for visible damage or wear.
- Check all connections and fasteners for security.
- Test the functionality of moving parts to identify any obstructions.
- Listen for any abnormal sounds during operation to pinpoint issues.
- Refer to the user manual for specific troubleshooting guidelines related to mechanical problems.
Signs of Damage and Possible Solutions
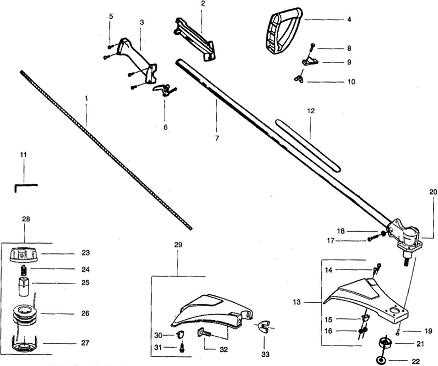
Identifying issues with your gardening equipment is essential for maintaining optimal performance and longevity. Recognizing specific indicators of wear and tear can help you take timely action to resolve potential problems. Below are some common signs of damage and their respective solutions.
-
Unusual Noises:
Any abnormal sounds during operation may indicate loose components or internal malfunctions.
- Inspect all connections for tightness.
- Check for foreign objects obstructing moving parts.
-
Reduced Performance:
If the equipment struggles to operate effectively, it may require attention.
- Examine the fuel supply and ensure it meets specifications.
- Replace any worn filters that could impede performance.
-
Excessive Vibration:
Increased vibration can signify misalignment or imbalance within the mechanism.
- Check for any bent or damaged components.
- Realign parts as necessary to ensure proper operation.
-
Visible Wear:
Cracks, dents, or corrosion can be indicators of significant wear.
- Replace damaged components promptly to avoid further issues.
- Regularly clean and maintain surfaces to prevent deterioration.
Taking proactive measures based on these signs can enhance the durability and functionality of your equipment. Regular maintenance checks will go a long way in ensuring smooth operation and preventing costly repairs.
|