Electrical System Breakdown for John Deere 112
The electrical configuration plays a critical role in ensuring the smooth operation of the machinery. Understanding the system’s layout and function is essential for maintaining reliability and preventing common malfunctions. The intricate wiring and connections are designed to support various operational tasks, providing power where needed and ensuring consistent performance across different components.
Key components of the electrical structure include the charging mechanism, ignition controls, and safety circuits. These elements work together to regulate power distribution, preventing overloads and ensuring that each section operates within optimal parameters. Proper maintenance of these systems can greatly extend the operational life of the machine, reducing downtime caused by electrical failures.
Routine inspections of the connections, wiring, and related electrical elements are crucial for identifying potential issues early. Keeping the system clean and free from corrosion can prevent short circuits and ensure a stable power supply during usage.
How the Steering Mechanism Works
The steering system plays a crucial role in guiding the vehicle, ensuring smooth and precise maneuverability. This mechanism connects the operator’s input to the wheels, allowing for efficient direction changes while maintaining control over the movement. Understanding its components and operation helps in maintaining and optimizing performance.
Main Components of the Steering System
The steering setup is made up of several key elements, each contributing to the overall function. The steering wheel is the main interface for the operator, transmitting force to the steering linkage that connects to the front axle. These parts work together to shift the wheels, directing the vehicle.
How Movement is Controlled
As the operator turns the wheel, the linkage system transfers this motion to the front wheels. The design ensures that both wheels turn simultaneously and at precise angles,
Examining the Hydraulic System Layout
The hydraulic system plays a crucial role in ensuring the smooth operation of various components within machinery. Understanding its layout is essential for maintenance and troubleshooting. The arrangement of hoses, valves, and pumps directs the flow of fluid, enabling precise control and movement across different mechanical sections. This section will break down the layout of these key elements, explaining how each contributes to overall functionality.
Key Components of the Hydraulic Setup
- Pumps: These generate the necessary pressure to circulate fluid throughout the system.
- Valves: Responsible for regulating fluid flow, ensuring the correct pressure is applied where needed.
- Hoses and Fittings: Provide the pathways for fluid transfer between different parts of the system.
Fluid Flow and Control Mechanisms
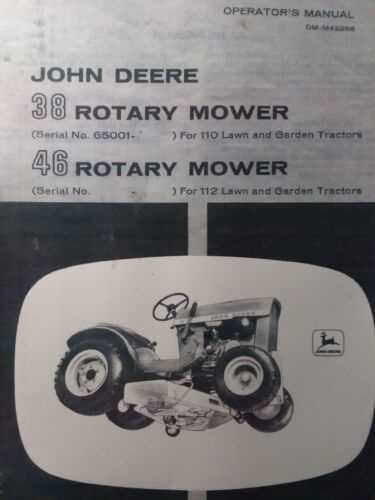
The direction and speed of hydraulic fluid movement are managed by a network of control mechanisms. These include pressure relief systems, directional valves, and return lines, all of which contribute to a balanced and efficient flow. Proper maintenance of these components ensures consistent performance and minimizes system wear over time.
Brake and Clutch Parts Analysis
The efficiency of machinery heavily relies on the functionality of its stopping and engagement mechanisms. Understanding the components that facilitate these operations is crucial for maintaining optimal performance and ensuring safety. A thorough examination of these elements reveals their significance in the overall system, highlighting the necessity for regular checks and timely replacements.
Braking System: The braking assembly consists of various components, each playing a vital role in decelerating the equipment. The primary elements include brake pads, rotors, and calipers. Wear and tear on these components can lead to decreased stopping power, posing potential risks during operation.
Clutch Mechanism: The engagement system is equally important, comprising parts such as clutch discs, pressure plates, and release bearings. These components work together to facilitate smooth transitions between power states. Ensuring they are in good condition is essential for preventing slippage and maintaining effective power transfer.
Regular inspections and maintenance of these systems not only enhance performance but also extend the lifespan of the machinery. Identifying and addressing wear issues promptly can save significant time and resources, ensuring that the equipment operates safely and efficiently.
Understanding the Fuel System Diagram
The fuel system is a crucial component of any engine, playing a vital role in ensuring proper operation and efficiency. This section delves into the intricacies of the fuel mechanism, illustrating how different elements work in harmony to deliver the necessary energy for optimal performance. A thorough grasp of this system can enhance maintenance practices and troubleshooting efforts.
Key Components: The fuel assembly comprises several essential elements, including the tank, pump, filter, and injectors. Each part serves a specific purpose, contributing to the overall functionality. For instance, the tank stores the fuel, while the pump is responsible for moving it through the system. Understanding these functions helps in identifying potential issues and implementing effective solutions.
Maintenance Tips: Regular inspection of the fuel components is vital for preventing malfunctions. Ensure that the filter is clean to avoid clogs, and check for leaks in the tank and lines. Keeping the fuel system in optimal condition not only prolongs the life of the engine but also improves performance and efficiency.
Seat and Frame Assembly Components
The seat and frame assembly is a crucial aspect of any machine, contributing to user comfort and structural integrity. This section explores the various elements that make up this assembly, ensuring optimal functionality and durability.
Key components include:
- Frame: The backbone that supports all other elements.
- Seat: Provides comfort for the operator, often designed for easy adjustments.
- Mounting brackets: Securely attach the seat to the frame.
- Support springs: Enhance comfort by absorbing shocks during operation.
- Seat belts: Improve safety by keeping the operator securely in place.
- Adjustment levers: Allow the user to modify the seat position effortlessly.
Understanding the role of each component ensures proper maintenance and replacement when necessary, contributing to a more efficient operation.
Tips for Replacing Commonly Worn Parts
Maintaining equipment is essential for ensuring optimal performance and longevity. Over time, certain components may experience wear and tear, leading to decreased efficiency. Knowing how to effectively replace these frequently affected elements can save time and money.
1. Identify Symptoms: Pay attention to any unusual sounds, vibrations, or changes in performance. These signs often indicate specific components that require attention. Regular inspections can help you catch issues early.
2. Refer to the Manual: Always consult the manufacturer’s guidelines for detailed information on part specifications and replacement procedures. This resource provides invaluable insights into the correct tools and methods required for each task.
3. Use Quality Replacements: Opt for high-quality substitutes that match or exceed the original specifications. Investing in durable components can enhance the overall performance and extend the life of the equipment.
4. Keep a Clean Workspace: Maintaining a tidy and organized environment can prevent damage to sensitive components during the replacement process. A clutter-free area allows for better focus and efficiency.
5. Test After Replacement: Once the worn components have been replaced, conduct a thorough test to ensure everything functions properly. Monitoring performance post-replacement is crucial for verifying the success of your maintenance efforts.