Component |
Engine Assembly Breakdown
The internal structure of the engine is a complex system where each component works together to ensure smooth operation. Understanding the detailed composition and how these elements interact can aid in both troubleshooting and maintenance. This section provides an in-depth look at the individual elements of the engine and their functions.
Main Components Overview
Key elements include the cylinder, piston, crankshaft, and connecting rod. These parts form the core of the engine’s performance, converting fuel into the power needed for efficient cutting. Each piece has its specific role, contributing to the engine’s overall efficiency and reliability.
Function and Interaction
The cylinder and piston work in harmony to create compression, while the crankshaft transforms this energy into rotational movement. The connecting rod links the piston to the crankshaft, allowing continuous motion. Together, these components ensure the engine operates at optimal levels.
Guide Bar and Chain Mechanism
The guide bar and chain form the core operational elements, designed to provide smooth and efficient cutting action. These components work in unison to ensure a stable and precise performance, balancing power and control. Understanding how they function together is crucial for maintaining optimal performance and safety during use.
Guide Bar Structure
The guide bar serves as the track for the cutting chain. Its durability and alignment are essential for ensuring a straight cut. Regular inspections of the guide bar help prevent wear, prolonging its lifespan and ensuring accurate cutting. Ensuring proper tension of the chain on the guide bar is equally important for safe operation.
Chain Mechanism Operation
The chain rotates around the guide bar at high speeds, making the cutting process efficient. It’s important to maintain sharpness and proper lubrication of the chain to reduce friction and extend the service life. Adjustments to chain tension should be done regularly to prevent slippage and improve safety during operation.
Fuel System and Carburetor Parts
The efficiency and performance of any cutting tool heavily depend on the proper functioning of its fuel system. A well-maintained fuel setup ensures that the engine receives the right mixture of air and fuel for optimal operation, leading to smoother performance and extended equipment life.
Main Components of the Fuel System
At the core of the fuel system lies the carburetor, which regulates the air-fuel ratio to maintain the engine’s performance. Other key elements include the fuel filter, fuel line, and fuel pump, each of which plays a crucial role in delivering clean fuel to the engine.
Common Issues and Maintenance Tips
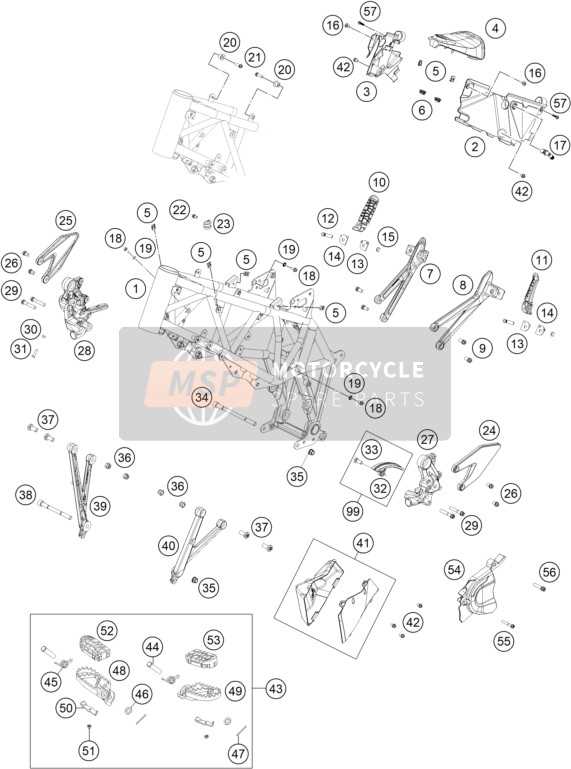
Proper maintenance of the fuel system is essential for ensuring longevity and preventing issues like clogging or air leaks. Regularly inspecting and replacing components such as the fuel filter and fuel line can help avoid operational problems, ensuring the system runs smoothly.
Ignition and Starter Components
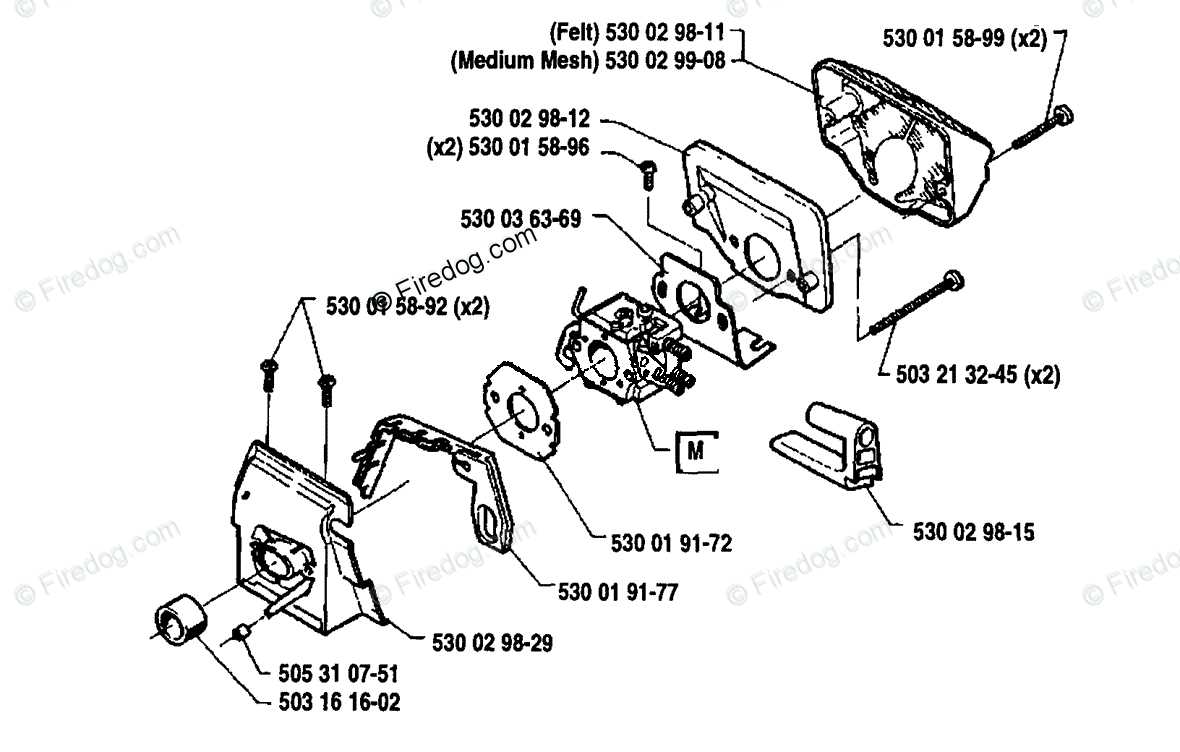
The ignition and starting mechanisms are crucial for ensuring that your cutting tool operates efficiently. These components work in tandem to initiate the engine’s combustion process, allowing for smooth performance and reliable functionality.
Ignition System plays a vital role in generating the spark needed for combustion. It typically includes elements such as the spark plug, ignition coil, and various wiring components. Each part contributes to delivering the electric current that ignites the fuel-air mixture within the combustion chamber.
Starter Assembly consists of components designed to facilitate the initial engine turnover. This assembly often features a recoil starter, pull cord, and associated mechanisms that ensure effortless engagement. Proper maintenance of these elements is essential to prevent starting difficulties and ensure longevity.
Handle and Vibration Dampening Systems
The design of modern cutting tools places significant importance on user comfort and efficiency. A well-engineered handle and effective vibration control mechanisms reduce operator fatigue, allowing for longer, more precise usage. These components are critical for maintaining control and reducing the strain on the user’s hands and arms during extended periods of operation.
Handle Design and Comfort
The handle is crafted to ensure a secure grip while minimizing slippage. Ergonomics play a key role, as the shape and material are specifically designed to fit comfortably in the user’s hand. A well-balanced handle not only improves control but also contributes to the overall ease of maneuvering.
Advanced Vibration Dampening
Vibration dampening systems are integrated into the tool to mitigate the effects of intense vibrations. This is especially important for reducing operator fatigue and ensuring long-term comfort. By isolating the vibrations from reaching the handle, these systems enhance operational safety while providing a smoother, more controlled experience.
Air Filter and Muffler Arrangement
The air filtration and exhaust system are key elements ensuring the optimal performance of any machine with an internal combustion engine. Proper maintenance of these components can significantly affect the machine’s efficiency, lifespan, and overall operational quality. The air filter keeps the engine free from dust and debris, while the muffler controls the exhaust flow and reduces noise emissions.
Air Filter Location and Function
The air filter is typically situated near the intake, filtering out harmful particles before they enter the engine. Regular cleaning or replacement is essential to prevent clogging, which could lead to performance issues or engine damage. A clean filter allows for smooth air intake, optimizing fuel combustion.
Muffler’s Role in Performance
The muffler is designed to manage the exhaust gases and reduce the noise generated during operation. It also helps in maintaining an appropriate pressure level in the exhaust system. Proper care of the muffler, such as checking for blockages or damages, can enhance efficiency and minimize harmful emissions.
Clutch and Chain Brake Structure
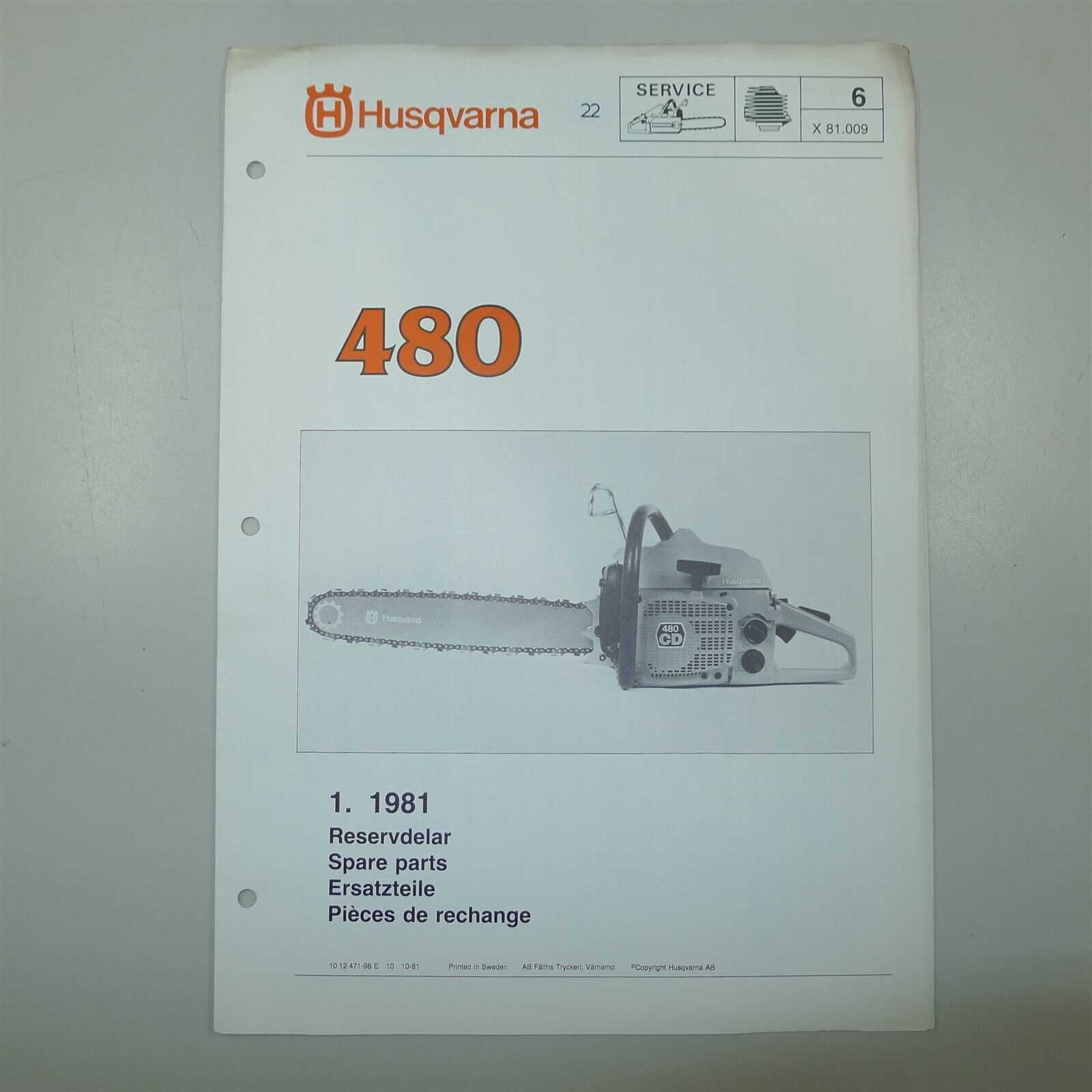
The mechanism responsible for managing the connection between the motor and the cutting tool plays a crucial role in ensuring operational safety and efficiency. This system not only facilitates the transfer of power but also includes features that help to halt the chain’s movement when necessary.
The clutch is designed to engage and disengage the engine’s power, allowing the tool to run without the chain spinning continuously. It consists of several components, including springs and shoes that work together to manage the rotational force. As the speed increases, the clutch engages, connecting the power source to the chain. Conversely, when the speed drops, it disengages, reducing the risk of accidental cuts during idle periods.
In addition, the chain brake serves as a vital safety feature. This component is engineered to stop the chain’s movement almost instantly if the tool experiences sudden kickback or if the operator activates the brake manually. The design usually involves a lever that, when triggered, applies friction to the chain, ensuring that it comes to a halt swiftly.
Overall, understanding the structure and functionality of the clutch and chain brake is essential for safe and effective operation, allowing users to maintain control while minimizing risks during use.
Maintenance Tips for Common Parts
Proper upkeep of various components in your equipment ensures longevity and optimal performance. Regular maintenance not only helps prevent breakdowns but also enhances the efficiency of the machinery. Below are essential tips for maintaining commonly found elements.
-
Lubrication:
Regularly apply lubricant to moving parts to minimize friction and wear. Ensure that the lubricant is suitable for the specific type of component.
-
Inspection:
Conduct routine checks for any signs of damage or wear. Look for cracks, corrosion, or any irregularities that could affect performance.
-
Cleaning:
Keep components clean from debris and dirt. Use a soft brush or cloth to wipe surfaces, ensuring no buildup interferes with functionality.
-
Tightening:
Periodically check that all fasteners are secure. Loose screws or bolts can lead to further complications and should be tightened as necessary.
-
Replacement:
Be proactive about replacing worn-out items. Timely replacement of damaged or ineffective parts can prevent more extensive repairs.
By following these maintenance practices, users can prolong the lifespan of their machinery and ensure reliable operation.