Moves the fuel
Cooling Mechanism and its Importance
The effective management of temperature within mechanical systems is crucial for optimal performance and longevity. A reliable cooling mechanism ensures that components operate within safe thermal limits, preventing overheating and subsequent failures. This system plays a vital role in enhancing efficiency and maintaining the integrity of machinery.
In many applications, heat is generated as a byproduct of friction and combustion. If not properly dissipated, this excess heat can lead to severe damage, including warping, cracking, or even complete breakdown. Therefore, understanding the various cooling strategies, such as liquid or air cooling, is essential for maintaining functionality and prolonging service life.
Additionally, an efficient cooling system contributes to energy savings by optimizing performance levels and reducing the need for frequent repairs. The selection of suitable cooling methods based on specific operational conditions can significantly impact overall productivity and operational costs. In summary, a well-designed cooling mechanism is fundamental for the reliability and efficiency of any machinery.
Ignition System Breakdown
The ignition mechanism plays a crucial role in ensuring the smooth operation of a power unit. It is responsible for generating the necessary spark to ignite the fuel-air mixture within the combustion chamber. Understanding its components and functionality can help in diagnosing issues and maintaining optimal performance.
Key Components
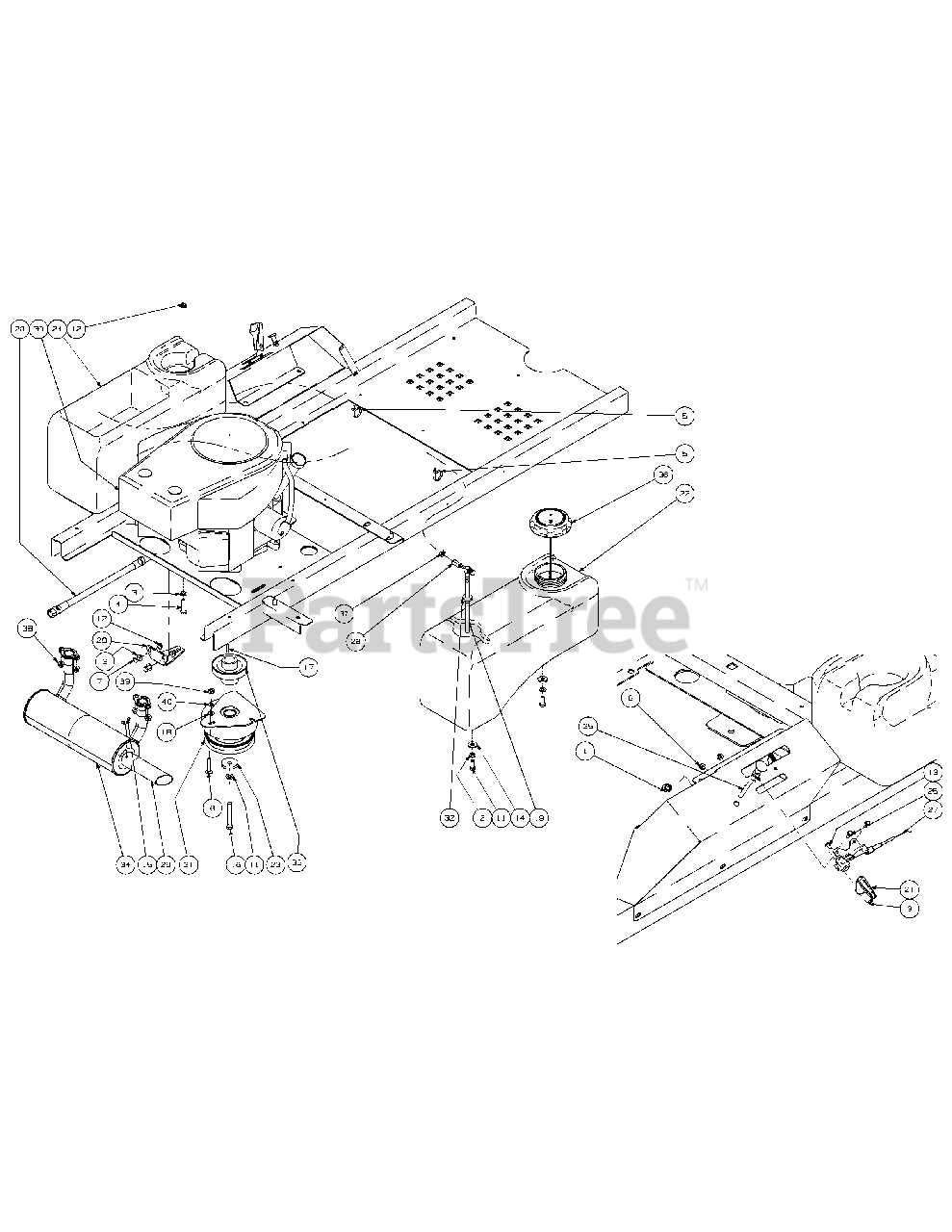
At the heart of the ignition system are several essential elements. The spark plug ignites the fuel mixture, while the ignition coil transforms low voltage from the battery into a high voltage required for sparking. The distributor, if present, directs the spark to the appropriate cylinder at the right time, ensuring efficient combustion.
Troubleshooting Common Issues
Identifying problems within the ignition setup can often be achieved through a systematic approach. Common symptoms include hard starting or misfiring, which may indicate a faulty spark plug or issues with the ignition coil. Regular inspections and timely replacements can help maintain a reliable ignition system.
Maintenance Tips for Engine Longevity
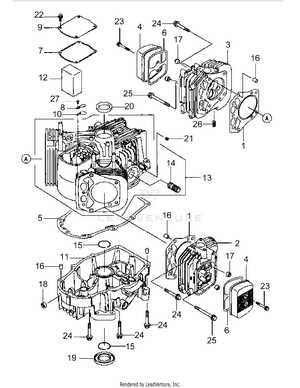
Ensuring the durability of your machinery requires consistent upkeep and attention to detail. Implementing routine checks and addressing issues promptly can significantly enhance performance and extend the lifespan of the components involved. Adopting a proactive approach not only prevents costly repairs but also maintains efficiency during operation.
Regular Oil Changes

Changing the lubricant at recommended intervals is crucial for reducing friction and preventing overheating. Fresh lubricant helps to keep all moving elements well-lubricated, minimizing wear and tear. It’s advisable to check the oil level frequently and ensure it meets the specifications outlined in the manual.
Inspecting Air Filters
Clean air filters are essential for optimal airflow and performance. Clogged filters can hinder performance and lead to engine inefficiencies. Regularly inspecting and replacing air filters ensures that the combustion process runs smoothly, ultimately promoting better functionality and fuel efficiency.
Common Issues and Troubleshooting
When dealing with small machinery, several frequent challenges can arise, impacting performance and reliability. Understanding these issues and their potential solutions is crucial for efficient operation and maintenance.
Frequent Problems
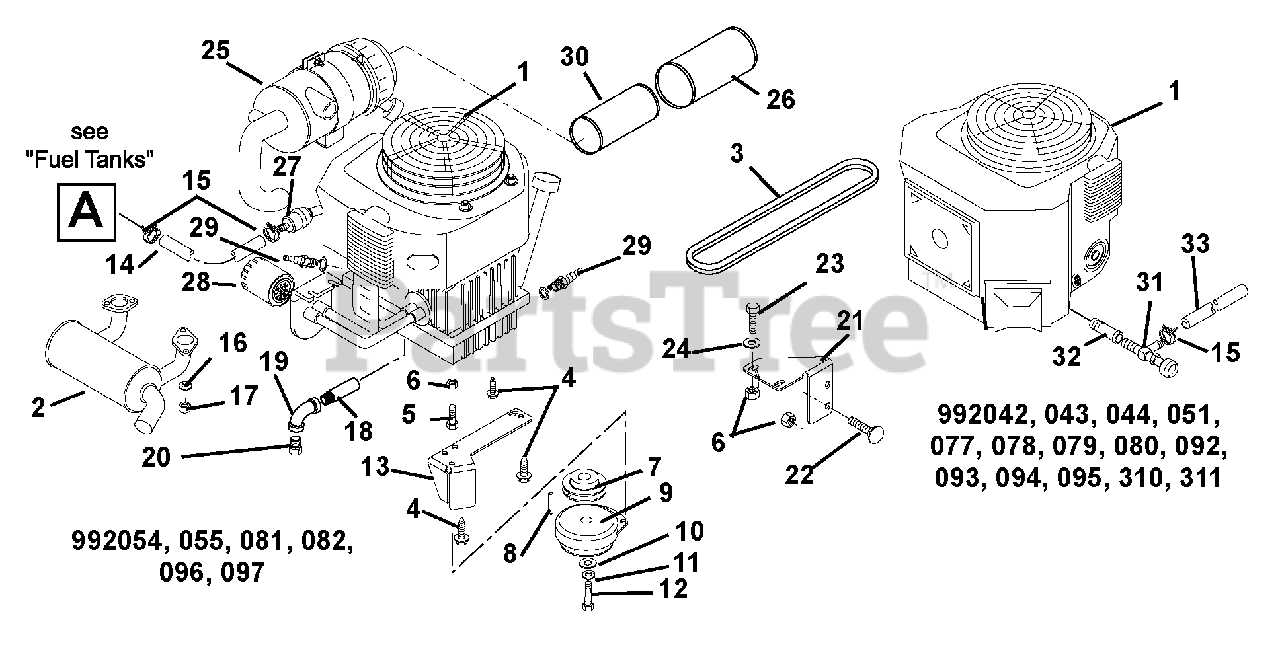
- Poor starting or failure to start
- Unusual noises during operation
- Overheating during use
- Inconsistent power output
- Fuel leaks or inefficient fuel consumption
Troubleshooting Tips
- Check the fuel level and quality. Ensure that you are using the appropriate fuel type and that it is not stale.
- Inspect the ignition system. Replace worn spark plugs or damaged ignition components as needed.
- Examine the air filter for blockages. A clean air filter is essential for optimal performance.
- Monitor for signs of overheating. Ensure that the cooling system is functioning properly, and check for any debris blocking airflow.
- Regularly service and lubricate moving parts to prevent wear and ensure smooth operation.
By addressing these common challenges proactively, operators can enhance the longevity and efficiency of their machinery.
How to Replace Worn Parts
Maintaining the performance of your machinery involves regularly checking for signs of deterioration and promptly replacing any damaged components. Identifying and addressing wear and tear not only enhances efficiency but also prolongs the lifespan of the overall system.
Identifying Worn Components
Before beginning any replacement process, it’s crucial to accurately identify which components require attention. Look for signs of wear such as cracks, unusual noises, or decreased performance. Regular inspections can help catch issues early, preventing more extensive damage.
Replacement Process
Once you have identified the worn components, gather the necessary tools and new replacements. Ensure that you follow the manufacturer’s guidelines for removing the old parts and installing the new ones. A strong attention to detail during this process will ensure a proper fit and optimal functionality. After installation, run the system to verify that everything operates smoothly, and perform any necessary adjustments.
Benefits of Using OEM Components
Utilizing original equipment manufacturer components ensures superior quality and compatibility for your machinery. These components are designed specifically for the intended application, offering optimal performance and longevity. By selecting OEM items, you can maintain the integrity of your system while minimizing the risk of failure due to inferior alternatives.
One significant advantage of OEM components is their reliability. They are subjected to rigorous testing and meet strict quality standards, which contributes to enhanced durability. This reliability translates to fewer repairs and reduced downtime, ultimately leading to cost savings in the long run.
Additionally, using OEM items helps preserve warranty coverage. Many manufacturers stipulate that only original components be used to maintain the validity of warranties. This protection can save you from unexpected expenses associated with repairs and replacements that might arise from using non-genuine parts.
Furthermore, OEM components often come with comprehensive support and documentation, which can be invaluable during installation and maintenance. Access to accurate information ensures proper handling and increases the likelihood of achieving optimal performance. Overall, investing in original components is a wise choice for anyone seeking efficiency, reliability, and peace of mind.
|