Adjustability |
Offers adjustable settings for both cutting height and conditioning pressure. |
Essential Components of the 5209 Discbine
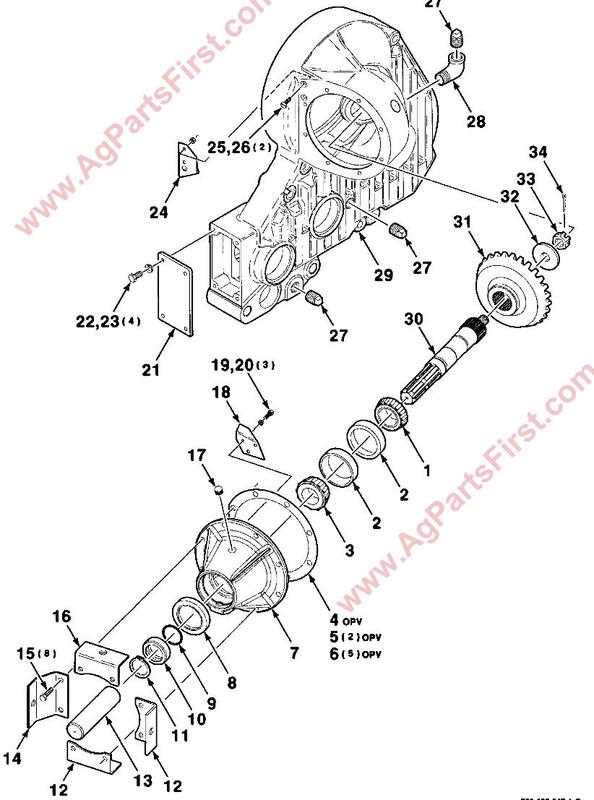
The functionality of this cutting machine relies on various crucial mechanisms working together. Each part plays a significant role in ensuring efficient performance, enabling smooth operation under demanding conditions. Understanding these components can help in maintaining the overall health and longevity of the equipment.
Cutting Blades form the backbone of the machine, designed for optimal cutting precision. These blades are engineered to withstand tough vegetation, ensuring clean and efficient cuts with every pass.
Drive Systems are another critical aspect, providing the necessary power and control for the operation. These systems ensure that the machine functions smoothly, transferring power to the necessary parts.
Lastly, protective shields are essential for ensuring both safety and durability. These elements protect the internal mechanisms from debris and external damage, prolonging the life of the machine while safeguarding the user.
Understanding the Cutter Bar Mechanism
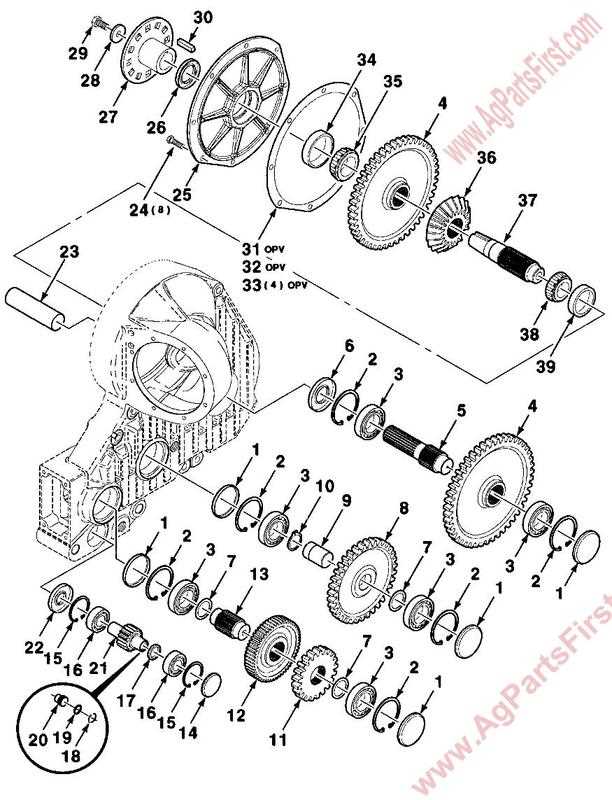
The cutter bar mechanism plays a vital role in the operation of hay cutting equipment. It consists of a series of coordinated components that work together to efficiently trim and process crops. By understanding how this system functions, operators can ensure better performance and longevity of the equipment.
Main Components and Their Roles
The cutter bar is designed to deliver precise cutting action through its blades, which are connected to a reciprocating motion system. Blades move back and forth to achieve clean cuts, while the supporting structure holds them in place and ensures consistent performance. Understanding each part’s role helps in maintaining optimal function.
Importance of Regular Maintenance
Maintenance is essential to keeping the cutter bar running smoothly. Regular checks and proper lubrication of the moving components reduce wear and tear, ensuring efficient operation over time. Neglecting this can lead to decreased cutting precision and equipment failure.
How the Drive System Operates
The drive system is a crucial component that transfers power from the engine to the cutting mechanism. Its efficient operation ensures the entire machine functions smoothly, enabling consistent performance during cutting tasks. Understanding the principles behind its operation can help maintain optimal functionality.
Power Transmission
Power generated by the engine is transferred through a series of interconnected components. This transmission occurs through a sequence of belts, gears, and shafts, each playing a role in distributing the energy required to operate the cutting mechanism.
- Belt System: The belt system helps deliver torque from the engine to other moving parts, ensuring smooth power distribution.
- Gears: Gears adjust the speed and torque as power moves through the system, allowing for precise control of the cutting speed.
- Shafts: Shafts serve as the final link, driving the cutting components to perform their task effectively.
Speed Control and Adjustments
Blades and Their Role in Performance
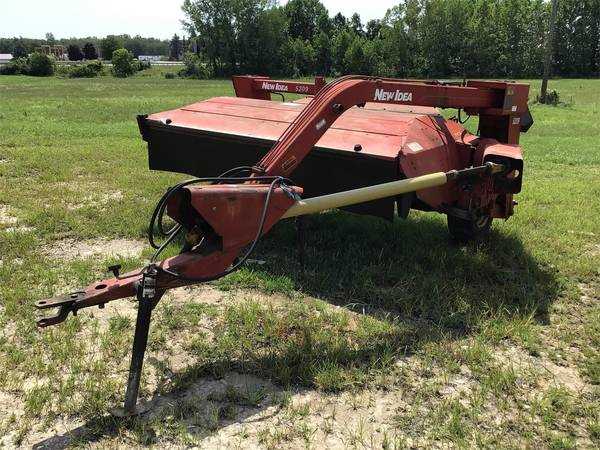
Blades play a crucial role in the efficiency and functionality of agricultural machinery. Their design, sharpness, and material directly influence how effectively crops are cut, impacting the overall speed and quality of the work. A well-maintained blade ensures smooth cutting and reduces strain on the equipment.
The type of blade used can also determine how cleanly and quickly the vegetation is processed. Whether dealing with tough or soft crops, the blades’ condition is key to maximizing performance and minimizing wear on the machine. Regular inspection and sharpening are essential for optimal operation.
Adjusting the Tension for Optimal Results
Proper adjustment of the tension is crucial for achieving the best performance and efficiency in your equipment. Ensuring the correct level of tension can enhance the quality of the work, reduce wear on components, and minimize downtime. Fine-tuning this setting will help the system operate smoothly under varying conditions, offering better results in both productivity and longevity.
Why Tension Matters
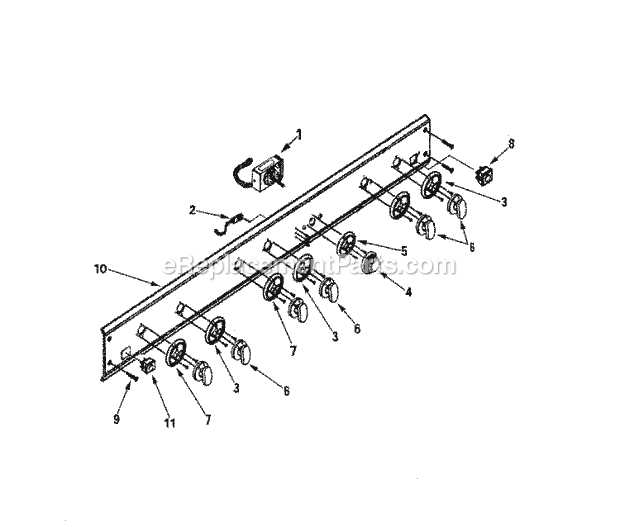
Maintaining the right amount of tension allows the equipment to function with maximum efficiency, ensuring that moving parts interact as intended. Too much or too little tension can lead to uneven performance, increased friction, and possible damage over time. A balanced adjustment helps keep everything in optimal alignment, which is key for smooth operation.
Steps to Achieve the Right Tension
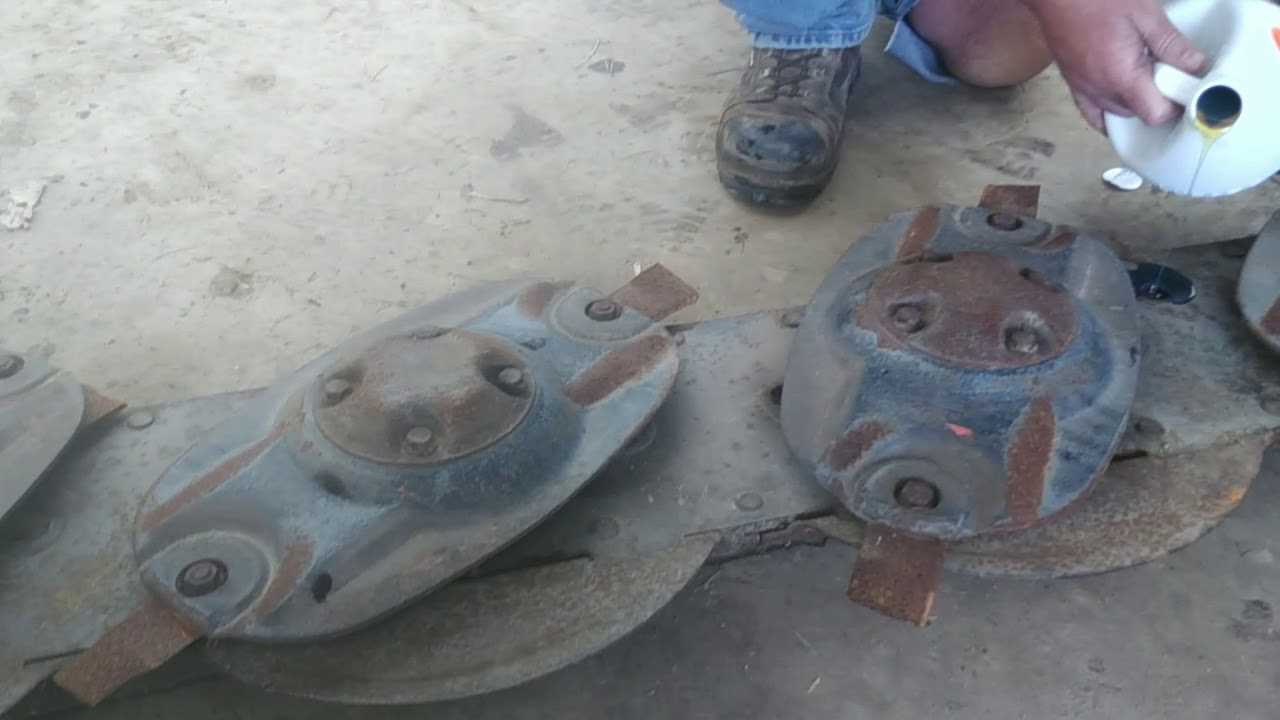
Begin by checking the manufacturer’s recommendations for tension settings. Adjust the tension gradually, monitoring the system’s response to ensure that it operates without strain or slack. Regular inspections and fine-tuning will help maintain consistent performance throughout the equipment’s lifespan.
Troubleshooting Common Issues with Parts
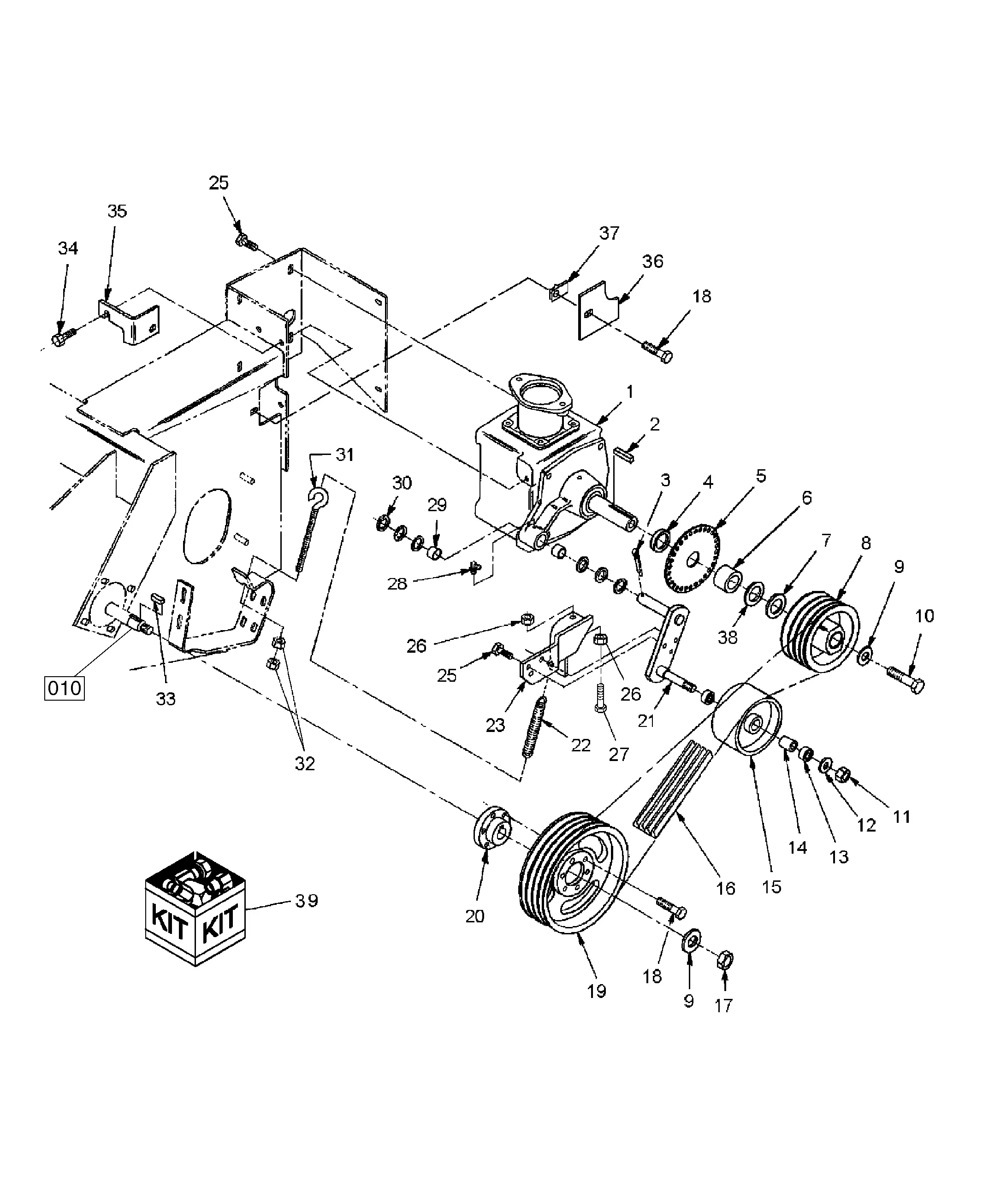
Understanding and addressing typical problems with mechanical components is essential for smooth operation. Identifying these issues early on can prevent more significant disruptions and ensure optimal functionality. By paying attention to common signs of wear and malfunction, you can keep equipment running efficiently.
Frequent Malfunctions: One of the most common concerns is the gradual wear of certain components, which can lead to poor performance. Pay close attention to any unusual noises, vibrations, or irregular movements, as these can be indicators of underlying issues.
Inspection Tips: Regular inspections are key to spotting potential problems before they escalate. Ensure that all connections are secure, and check for any signs of damage such as cracks or excessive friction. Keep an eye on lubrication levels to avoid unnecessary strain on the moving parts.
Maintenance Advice: Maintaining components properly is crucial for longevity. Use recommended cleaning products and lubricants, and replace worn-out pieces as soon as possible. Keeping a record of any repairs or replacements can help you anticipate future needs and avoid unexpected breakdowns.
Maintenance Tips for Longevity
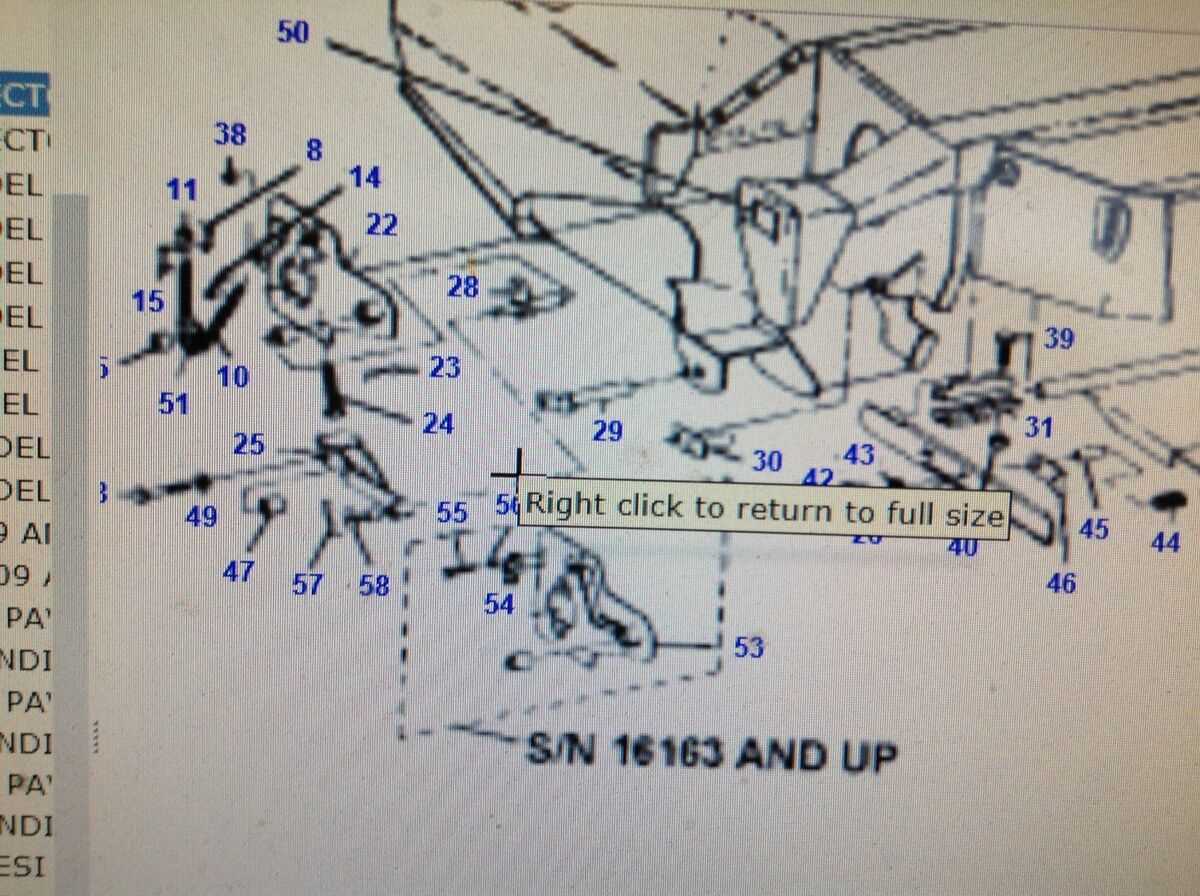
To ensure your equipment operates efficiently for years, regular upkeep is essential. Consistent care not only enhances performance but also prevents premature wear and costly repairs. By following a few key practices, you can extend the lifespan of your machinery and optimize its functionality.
1. Regular Inspection: Check all moving components for signs of wear and tear. Inspect for loose connections, rust, and any irregularities that might hinder performance. Addressing small issues early can prevent bigger problems later on.
2. Proper Lubrication: Ensure that all mechanical parts are properly lubricated. Regularly applying the right type of lubricant reduces friction and minimizes unnecessary stress on components, prolonging their life.
3. Clean Thoroughly: Keep the equipment free from dirt, debris, and other contaminants. Clean components after each use to prevent build-up that can lead to clogs or damage. A clean machine runs smoother and more efficiently.
4. Follow Manufacturer Guidelines: Always adhere to the maintenance schedule recommended by the manufacturer. This includes replacing worn-out parts and checking for updates on recommended maintenance practices.
5. Store Properly: When not in use, store your equipment in a dry, sheltered location to avoid exposure to the elements. Protecting it from extreme weather conditions can prevent rust and other forms of degradation.
Finding Reliable Replacement Parts
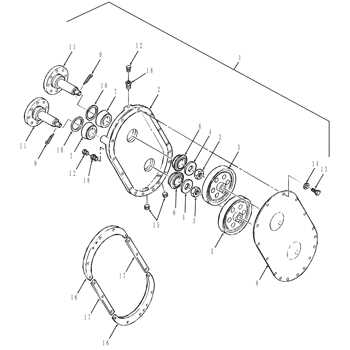
When maintaining agricultural machinery, ensuring high-quality components is essential for optimal performance and longevity. A dependable source for acquiring the right components can prevent costly repairs and downtime. It is important to choose parts that match the specifications and are designed to withstand the demands of your equipment.
Evaluating Quality and Durability
Before purchasing any component, evaluate its quality and durability. Consider sourcing items from reputable manufacturers or suppliers who offer a proven track record of reliable products. Always verify the material used and its compatibility with your machine’s requirements to avoid premature wear and tear.
Where to Find Trusted Sources
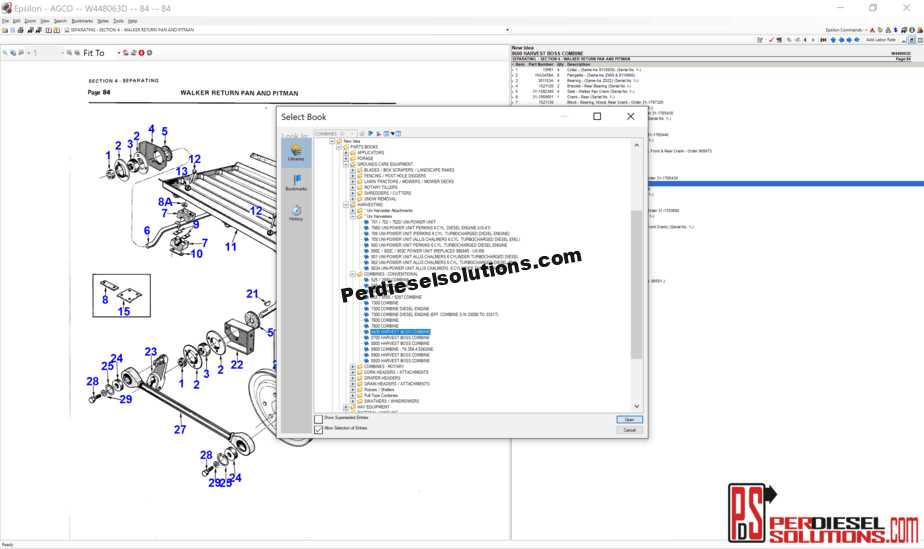
Trusted suppliers often offer warranties or guarantees for their products, ensuring peace of mind when replacing key elements. You can also explore online reviews and user feedback to gauge the performance and reliability of different brands. It’s always recommended to choose vendors that specialize in agricultural machinery, as they tend to offer parts that are both robust and perfectly suited to the tasks at hand.