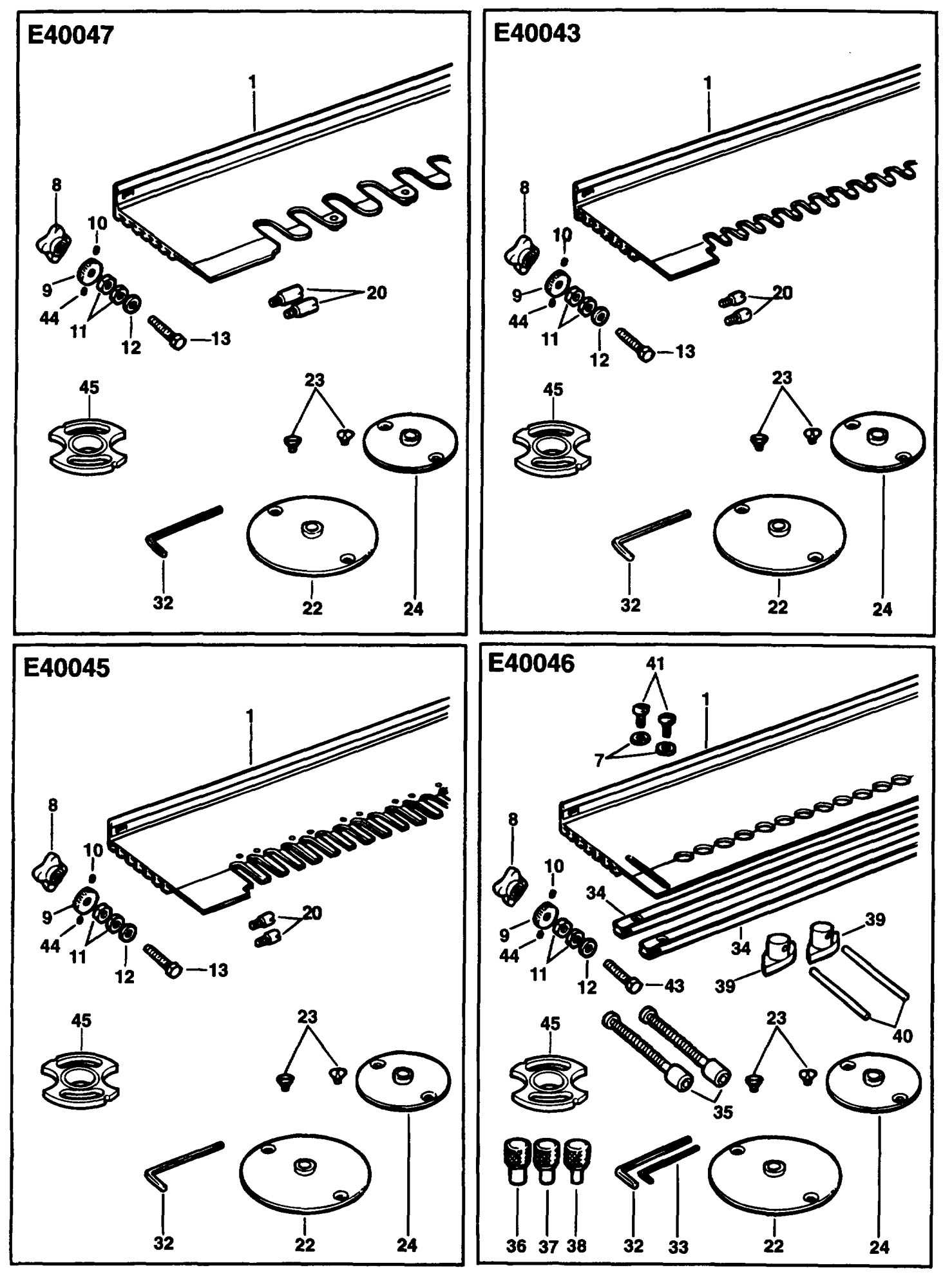
In the world of farming, reliable equipment is essential for ensuring efficient operations and maintaining high productivity. One of the most important tools in this sector is the machinery used for cutting and harvesting. These machines are designed with a variety of interconnected elements that work together to perform their tasks smoothly and effectively.
Each component in these cutting tools serves a specific function, contributing to the overall performance. Understanding how these pieces fit and operate is crucial for both maintenance and troubleshooting. This guide will provide an in-depth look into the various elements of the cutting mechanism, helping users navigate the structure of agricultural equipment.
Whether you are a seasoned professional or new to farming, having a clear grasp of the mechanics involved in your tools can make a significant difference. This section will explore the essential features, providing you with the knowledge needed to keep your machinery running at its best.
Overview of Fort Disc Mower Components
Understanding the key elements of this agricultural equipment is essential for ensuring smooth operation and proper maintenance. Each component plays a vital role in delivering efficient grass cutting, and knowing how they work together helps with troubleshooting and repair. This section provides a detailed look at the various units that make up the machinery, from cutting elements to drive systems.
Cutting Mechanism
The cutting mechanism is the heart of the machine. It includes rotating blades mounted on discs, which operate in tandem to cut vegetation at ground level. These blades are designed to deliver precision and efficiency, ensuring clean cuts even in dense or wet conditions. The spacing and arrangement of the blades are critical for optimal performance.
Drive and Transmission System
The drive system transfers power from the engine to the cutting components. It includes shafts, gears, and bearings that work together to synchronize movement and ensure that the cutting action is continuous and smooth. The durability and alignment of these parts are crucial for preventing breakdowns and ensuring longevity.
Maintenance Tip: Regular inspection of the drive components is essential to prevent wear and tear, which can lead to costly repairs or reduced efficiency.
Understanding the Cutter Bar System
The cutter bar is a critical component of any cutting equipment, playing a fundamental role in the precision and efficiency of the cutting process. Its design ensures smooth and effective performance in a wide range of field conditions. In this section, we will explore how the system operates, the main elements involved, and how they work together to deliver consistent results.
Main Components of the Cutter Bar
At its core, the cutter bar system consists of several essential parts that interact seamlessly to achieve accurate cutting. Each part serves a specific purpose and contributes to the overall functioning of the machine.
- Blades: These sharp, rotating elements are responsible for slicing through materials with precision.
- Guards: Positioned to protect the blades and guide the material into the cutting zone.
- Drive Mechanism: The system that powers the movement of the blades, ensuring consistent speed and cutting action.
How the System Works
The process begins as the blades move at high speeds, cutting through the material that is directed
Identifying Key Gearbox Parts
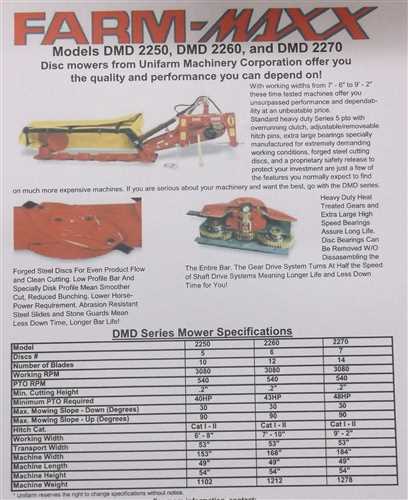
The gearbox plays a crucial role in transforming mechanical energy within various machines. Understanding its internal components can help ensure smooth operation and timely maintenance. Below we will examine the primary elements found inside most standard gearboxes, highlighting their functions and importance in overall performance.
Main Components
Several essential parts form the core of a gearbox. Each of them contributes to transferring power and motion effectively. These components vary in complexity but work in unison to ensure optimal energy transmission and regulation.
Component |
Function |
Input Shaft |
Receives power from an external source and transfers it to the internal gears. |
Gears |
Responsible for modifying speed and torque by engaging with other gears of different sizes. |
Bearings |
Supports rotating parts, reducing friction and wear inside the gearbox. |
Blade Assembly and Maintenance Tips
Proper setup and regular upkeep of your cutting tool are crucial for ensuring longevity and optimal performance. Maintaining the sharpness and balance of the blades helps avoid unnecessary wear, reduces strain on the machine, and results in a cleaner cut. Below, we discuss key aspects of assembly and maintenance to keep your equipment running smoothly.
Assembling the Blades
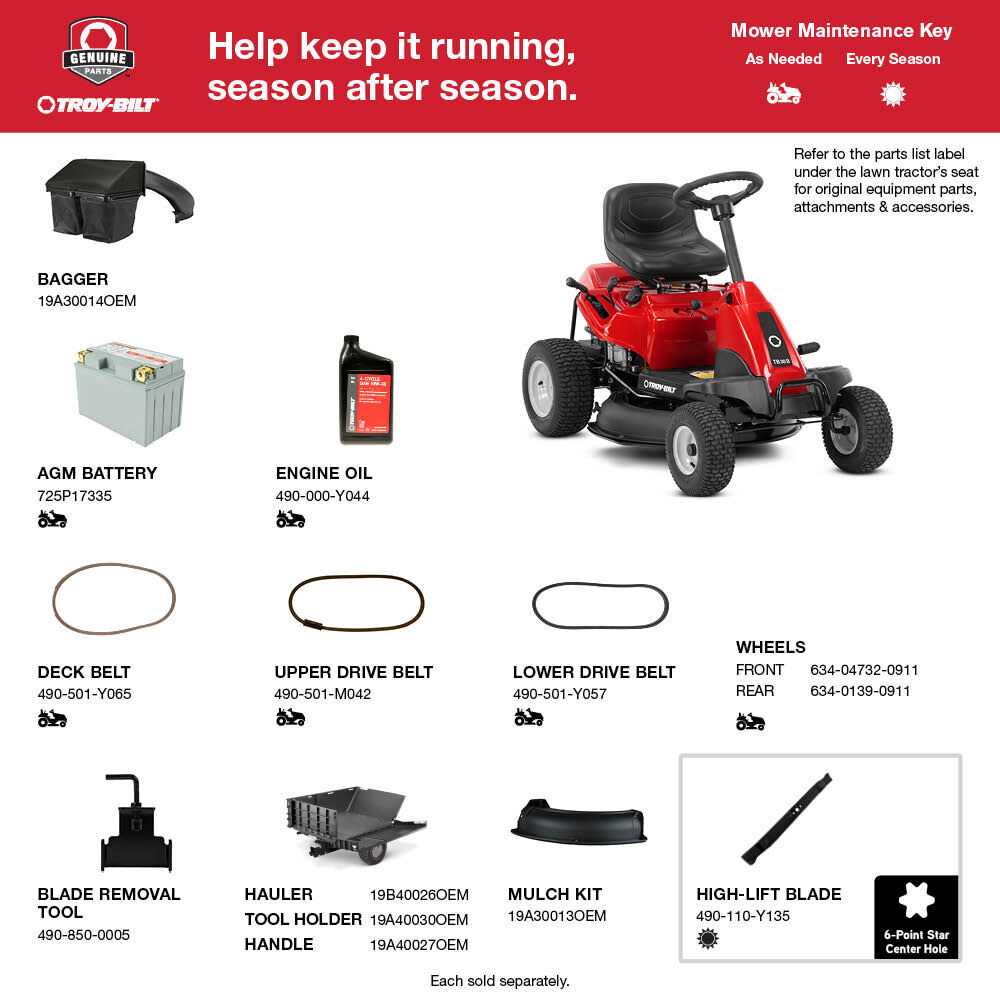
When installing blades, ensure they are correctly aligned to avoid imbalance. Misalignment can lead to vibrations and faster component wear. Use the recommended bolts and fittings, securing them tightly to avoid any movement during operation.
- Align blades following the manufacturer’s guidelines.
- Double-check for any wobble or looseness before operation.
- Ensure all bolts and screws are properly tightened.
Maintenance Tips
Regular maintenance extends the life of your cutting tool and ensures efficient operation. Dull blades increase fuel consumption and may damage the vegetation being cut. Follow these simple steps to maintain your blades in top condition:
- Sharpen blades frequently to maintain cutting efficiency.
- Inspect for signs of wear or damage,
How to Replace Drive Shafts
Replacing the drive shaft is a critical maintenance task that ensures the machine operates smoothly and efficiently. Over time, wear and tear can cause the shaft to degrade, leading to performance issues or potential breakdowns. This section will guide you through the process of safely removing the old shaft and installing a new one, ensuring the equipment continues to function optimally.
Begin by disconnecting the power source to prevent accidental activation. Next, inspect the area around the shaft for any components that need to be removed or loosened, such as guards or mounting bolts. Carefully detach these parts to access the shaft fully.
Once the surrounding components are out of the way, locate the connections that hold the shaft in place. These may include splines, couplings, or locking pins. Use the appropriate tools to disengage these fasteners, making sure to support the shaft as it is removed to prevent any damage or injury.
After removing the old shaft, take the time to clean the mounting points and check for any signs of damage or wear on adjacent parts. Proper cleaning ensures a smooth installation of the new shaft, while inspecting the surrounding area helps prevent future issues.
To install the new drive shaft, align it with the mounting points, making sure it fits snug
Guide to Mower Conditioning Rollers
The conditioning rollers play a crucial role in the efficiency and effectiveness of grass management equipment. These components ensure that the cut material is processed properly, promoting faster drying and enhancing overall crop quality. Understanding the design, function, and maintenance of these rollers is essential for optimizing performance and prolonging the lifespan of the machinery.
Types of Conditioning Rollers
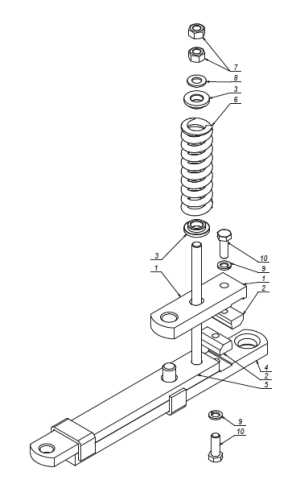
Conditioning rollers come in various configurations, each suited for specific tasks and conditions. The most common types include rubber and steel rollers, which provide distinct advantages in terms of operation and results. Rubber rollers are designed to gently crimp the forage, minimizing leaf loss and preserving nutritional value. In contrast, steel rollers offer more aggressive conditioning, which is beneficial for tougher crops.
Maintenance Tips
Regular maintenance of conditioning rollers is vital to ensure optimal performance and longevity. It is important to inspect the rollers for wear and tear, as well as for any debris that may hinder their function. Keeping the rollers clean and well-lubricated can significantly improve their efficiency. Additionally, checking the alignment and tension is essential to prevent uneven wear and potential damage during operation.
Functionality of Safety Shields and Covers
Safety shields and covers play a crucial role in ensuring the secure operation of agricultural machinery. These protective elements are designed to minimize the risk of injury by enclosing moving components, thereby preventing accidental contact. Their importance cannot be overstated, as they significantly contribute to the overall safety and reliability of equipment during use.
One of the primary functions of these shields is to act as a barrier between the operator and potentially hazardous parts. By effectively shielding users from sharp edges and rotating elements, they reduce the likelihood of accidents. Additionally, covers help contain debris and materials, ensuring a cleaner working environment and enhancing visibility.
Moreover, safety shields and covers are integral to maintaining machinery efficiency. They help protect vital components from dirt, dust, and moisture, which can lead to wear and tear. This not only extends the lifespan of the equipment but also ensures it operates at peak performance, ultimately leading to increased productivity in agricultural tasks.
Common Wear and Tear Parts to Inspect
Regular maintenance is crucial for ensuring the longevity and efficiency of your equipment. Over time, various components may experience degradation due to prolonged use and exposure to harsh conditions. Identifying and addressing these areas of wear can help prevent more significant issues down the line, thereby saving time and money.
Blades and Cutting Edges
The cutting implements are among the most frequently subjected to wear. They should be examined for signs of dullness, chipping, or deformation. Regular sharpening or replacement of these elements is essential for optimal performance and effectiveness in operation.
Belts and Drive Systems
Drive components play a vital role in transferring power throughout the machinery. Inspecting belts for fraying, cracking, or excessive slack is essential. Ensuring these elements are in good condition helps maintain consistent performance and reduces the risk of unexpected breakdowns.